Kinh nghiệm tiết kiệm 30% điện năng tiêu thụ của lò nung clinker (P1)
(ximang.vn) Trong những năm gần đây, ngành xi măng toàn châu Âu đã trải qua một giai đoạn chuyển đổi để tăng cường hiệu quả sử dụng nhiên liệu trong lò nung clinker. Hơn nữa, nhiệt năng của khí thải lò đã được tận dụng nhiều hơn cho sấy sơ bộ nguyên liệu và nhiên liệu cấp, cùng với việc tối ưu hóa các hệ thống làm nguội clinker để thu hồi được nhiều nhiệt hơn đưa trở lại lò nung, tất cả đã mang lại kết quả là giảm tiêu hao nhiên liệu.
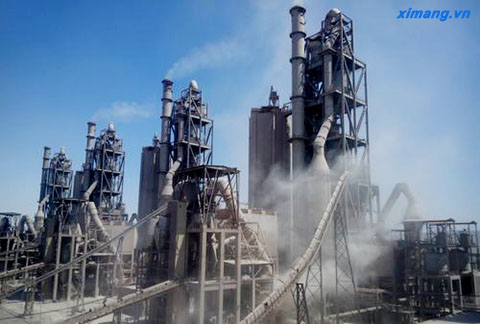
WHR là công nghệ tốt nhất hiện nay có thể tiết kiệm đến 30% điện năng tiêu thụ khi vận hành một lò nung clinker.
Việc cải thiện hiệu suất hệ thống nhiệt cho phép giữ nguyên lượng nhiệt năng hiện có, trong khi có thể xếp hệ thống vào loại cấp độ thấp (về tiêu thụ năng lượng), vì nhiệt độ khí thải thấp hơn nhiều so với 300oC. Ngoài ra, các quạt tiêu thụ thêm điện năng sẽ làm giảm thấp hơn nữa nhiệt độ của dòng gió đi vào hệ thống lọc bụi, trong hệ thống cấp độ thấp này.
Những cải thiện về hiệu suất nhiệt khiến cho lượng nhiệt năng dư thừa được xem là loại nhiệt năng ‘cấp thấp’ vì nhiệt độ khí thải thấp hơn nhiều so với 300oC. Năng lượng điện bổ sung bị tiêu hao bởi các quạt làm giảm thêm nhiệt độ của nhiệt cấp thấp này trước khi nó đi vào các hệ thống lọc bụi.
Do sức ép của các bên có liên quan tới ngành xi măng đối với việc giảm bớt phát thải khí carbon, việc thu hồi nhiệt thải cấp thấp này bằng các hệ thống thu hồi nhiệt khí thải (Waste Heat Recovery - WHR) tích hợp để phát điện với mức carbon thấp đang ngày càng được xem xét đến dựa vào mức hoàn vốn đầu tư.
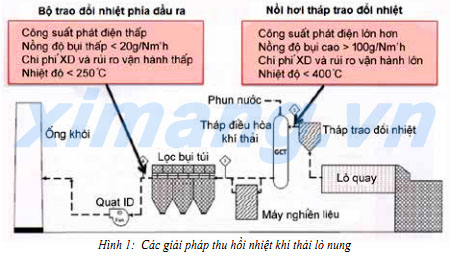
Các công nghệ WHR đang được phát triển để giảm bớt chi phí lắp đặt cho 1 kW công suất phát điện, và thêm vào đó là lợi ích từ việc giảm tiêu thụ điện năng của các quạt lọc bụi, dẫn đến chỉ số hoàn vốn đầu tư được cải thiện. Bài viết này sẽ giới thiệu với bạn đọc về những thách thức trong tích hợp WHR và các kỹ thuật công nghệ tốt nhất hiện có mà có thể tiết kiệm đến 30% điện năng tiêu thụ khi vận hành một lò nung clinker.
Các vị trí tích hợp WHR
Có 03 vị trí chủ yếu trong dây chuyền xi măng có thể thu hồi nhiệt khí thải, bao gồm:
- Hệ thống trao đổi nhiệt/ Sấy sơ bộ: từ khí thải của tháp trao đổi nhiệt phía sau lò quay. Khí thải đi ra từ lò nung có nhiệt độ cao, đi qua các tầng cyclone khác nhau để gia nhiệt cho nguyên liệu. Phần lớn các nhà máy đều lắp đặt một tháp điều hòa khí thải (GCT), tại đây, khí thải được làm nguội đến nhiệt độ yêu cầu trước khi đưa trở lại máy nghiền liệu hoặc máy nghiền than, và phải đáp ứng các điều kiện đầu vào của hệ thống lọc bụi. Đây là vị trí có thể thu hồi được lượng nhiệt năng lớn nhất.
- Dòng khí thải phía Đầu Ra (Tail End - TE) sau lọc bụi túi hoặc lọc bụi điện cung cấp một nguồn nhiệt có nhiệt độ thấp, nhưng dòng khí này có hàm lượng bụi rất thấp so với các vị trí khác trên dây chuyền. Thu hồi nhiệt năng ở đây ít bị rủi ro hơn về mặt công nghệ nhưng điện năng phát ra cũng thấp hơn.
- Thiết bị làm nguội đột ngột bằng khí (Air Quench Cooler – AQC): clinker ra khỏi lò nung được vận chuyển qua hệ thống làm nguội clinker để làm nguội. Khí thải đi ra từ máy làm nguội clinker cung cấp một nguồn nhiệt năng ở thể khí nóng khô có thể thu hồi được và sử dụng để phát điện theo công nghệ WHR. Nhiệt độ đặc trưng của dòng khí nóng thoát ra từ clinker ở vào khoảng 300oC. Thông thường, dòng khí nóng được làm mát thêm bằng phương pháp làm mát trực tiếp hoặc gián tiếp, để tránh đưa dòng khí có nhiệt cao đi vào lọc bụi tĩnh điện hoặc lọc bụi túi. Nhiệt thải thu hồi được phía trước Lọc bụi tĩnh điện, lọc bụi túi có thể sử dụng để phát điện và cũng mang lại lợi ích nữa cho nhà máy nhờ giảm bớt tiêu thụ điện năng tại các quạt trao đổi nhiệt khí và quạt của lọc bụi chính (quạt ID).
Các thách thức về tích hợp
Khi tích hợp một hệ WHR, cần xem xét tới các khía cạnh về thiết kế chính sau đây:
♦ Giảm thiểu các rủi ro cho dây chuyền công nghệ
Thiết kế phải bảo đảm cho hệ thống vận hành an toàn tin cậy, có khả năng cách ly hoàn toàn với dây chuyền hiện tại khi hệ WHR không hoạt động. Bằng cách định vị thiết bị trao đổi nhiệt của hệ thống thu hồi nhiệt trên đường ống phân nhánh (bypass) và sử dụng hệ điều khiển tự động để điều khiển các van điều tiết lưu lượng chính, để chuyển hướng dòng khí thải giữa đường ống của hệ thống WHR và đường ống chính; quy trình sản xuất vận hành độc lập với vận hành hệ WHR.
♦ Lượng bụi trong khí thải
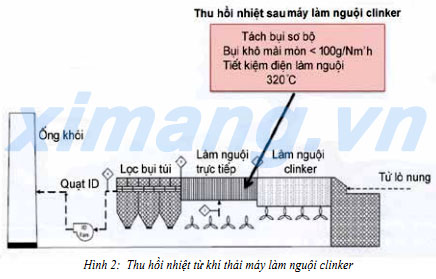
Lượng bụi có trong khí thải có thể gây đóng bám và tắc nghẽn khi chúng tích tụ trên các đường ống của thiết bị trao đổi nhiệt. Điều này có thể làm gia tăng độ sụt áp suất đối với quạt ID cần phải khác phục và làm giảm hiệu suất thiết bị trao đổi nhiệt. Thiết kế của thiết bị trao đổi nhiệt là phần then chốt để tạo lập ra một hệ thống tin cậy với tuổi thọ vận hành kéo dài. Một hệ thống làm sạch đường ống thiết bị trao đổi nhiệt, phù hợp với các đặc tính riêng của bụi tại nhà máy, là cần thiết. Bụi từ khí thải máy làm nguội clinker và từ khí thải tháp trao đổi nhiệt có những đặc tính khác nhau. Nhìn chung, đặc tính của bụi từ hệ thống làm nguội clinker là cứng và có tính mài mòn, trong khi đó bụi từ lò nung có hạt nhỏ, mịn và có tính bám dính. Thành phần hóa học của các dòng khí thải này cũng có khác biệt rất lớn. Vì vậy, thiết kế hệ thống thu hồi nhiệt thải cho các dòng khí này phải được xử lý khác nhau. (Hình 2)
♦ Sụt áp suất trên hệ thống thu hồi nhiệt
Việc lắp đặt thiết bị trao đổi nhiệt khí thải và các đường ống bổ sung trong dây chuyền công nghệ sẽ làm tăng độ sụt áp suất trong hệ thống. Độ sụt áp suất hệ thống tăng lên đòi hỏi tiêu thụ điện năng của quạt tăng lên. Lượng điện năng tiêu thụ của quạt, do kết quả của việc tăng áp suất hệ thống (dẫn đến làm giảm tỷ lệ lưu lượng dòng gió nóng đi từ thiết bị làm nguội vào hệ thống), cần phải được xem xét kỹ càng khi thiết kế. Giảm thiểu độ sụt áp suất là một vấn đề mấu chốt, nhằm tránh phát sinh thêm chi phí nâng cấp quạt ID cho dự án. Việc sử dụng phần mềm máy tính để mô hình hóa động học dòng chảy (CFD), nhằm tối ưu hóa hình dạng kết cấu khi thiết kế thiết bị trao đổi nhiệt và đường ống phân nhánh là một công cụ thiết yếu để thu hẹp biên độ của sụt áp.
♦ Tính mài mòn, ăn mòn thiết bị trao đổi nhiệt và sự ngưng tụ của khí thải
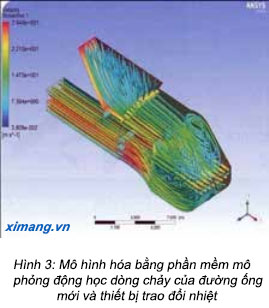
Mỗi nhà máy có các đặc tính khác nhau về sản phẩm, nhiên liệu sử dụng, và kiểu thiết kế lò nung. Việc sử dụng các kỹ thuật tốt nhất hiện có để mô phỏng các chế độ phụ tải bụi, cũng như sự phân bố nhiệt độ và dòng khí, là cần thiết khi thiết kế thiết bị trao đổi nhiệt, nhằm đạt được tuổi thọ vận hành và hiệu suất lớn nhất. Vì vậy, khi thiết kế một hệ WHR cần phải cân nhắc, xem xét đến tất cả các công nghệ, kỹ thuật tốt nhất hiện có để tối ưu hóa chi phí, tuổi thọ vận hành, độ tin cậy và hiệu quả tổng thể của hệ thống.
Quỳnh Trang (Theo TTKHKT Xi măng)