Hệ điều khiển PLC - Biến tần - Động cơ không đồng bộ ba pha (P2)
Trong các nhà máy xi măng, chúng ta thường gặp bộ ba: Bộ điều khiển lô gíc có thể lập trình (PLC-Programmable logic controller) - biến tần - động cơ nhưng mối quan hệ điều khiển của bộ ba này xảy ra nhưng thế nào? Vai trò của nó ra sao ? Bài viết sau đây sẽ một phần nào đó làm sáng tỏ vấn đề nêu trên.
>> Hệ điều khiển PLC - Biến tần - Động cơ không đồng bộ ba pha (P1)
2. Điều chỉnh ổn định tốc độ động cơ của PLC
Trong phần này, chúng ta sẽ tìm hiểu quá trình điều khiển bám theo vị trí và tốc độ động cơ của hệ truyền động PLC - Biến tần - động cơ.
PID là bộ điều khiển kín được coi là lý tưởng đối với các tham số các bộ điều khiển liên tục. Kết hợp giữa các bộ điều khiển tỷ lệ - tích phân - vi phân, PID được coi là bộ điều khiển động mà việc thay đổi tham số của bộ điều khiển có khả năng làm thay đổi các đặc tính động và đặc tính tĩnh của hệ điều khiển tự động.
Hình 6: Điều khiển với bộ điều khiển PID
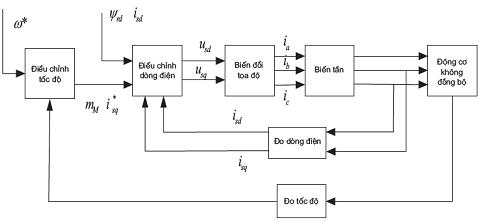
Hình 7: Các vòng điều khiển trong hệ truyền động điện
Đặc biệt trong hệ điều khiển PLC - biến tần - động cơ, để thấy rõ được vai trò của bộ điều khiển PID trong quá trình điều khiển ổn định tốc độ và vị trí góc của hệ này, dựa trên những thông tin phần trên, ta tiến hành xây dựng mô hình điều khiển dựa trên công cụ có sẵn Matlab. Theo sơ đồ cấu trúc hình thu thập giá trị đặc tính bám của hệ thống trước và sau khi có bộ điều chỉnh PID.
Từ đó, ta có mô hình bài toán điều khiển bám động cơ không đồng bộ ba pha theo phương pháp tựa theo từ thông roto:
a. Xây dựng mô hình điều khiển bám trong Matlab
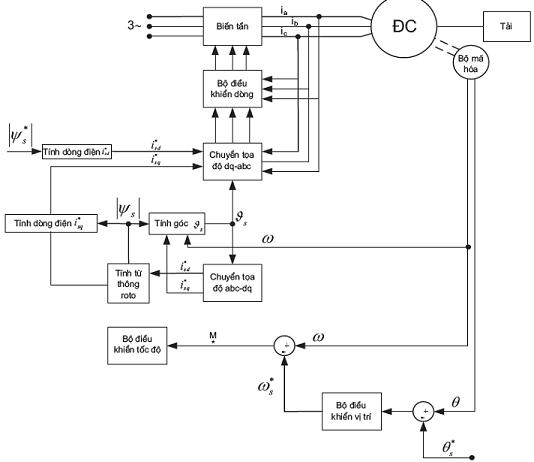
Hình 8: Mô hình điều khiển động cơ không đồng bộ định hướng từ thông roto
Các khối có sẵn ta lần lượt xây dựng các khối điều khiển: vị trí, biến tần, khối nguồn trong thư viện của Matlab. Hệ thống thực hiện vòng điều chỉnh phản hồi: dòng điện, mô men, tốc độ, vị trí.
Quá trình điều khiển như sau:
Khi có tốc độ chuẩn từ khối điều khiển vị trí đưa vào, tốc độ của động cơ được tính toán qua khối tính dòng i*sq, tốc độ thực tế của động cơ đo được đưa đến bộ điều chỉnh tốc độ, bộ tính toán từ thông được chuyển đổi thành các dòng điều khiển theo trục dq và trục αβ đưa đến bộ điều chỉnh dòng vào đưa ra tín hiệu xung điều khiển đóng mở bộ nghịch lưu có điều khiển trong khối biến tần. Thực tế, các khối điều khiển tốc độ, vị trí góc được xây dựng từ các hàm tỷ lệ - tích phân - vi phân dựa trên sơ đồ cấu trúc trên.
Thực hiện mô phỏng và điều chỉnh các tham số bộ PID ta có kết quả như sau với thời gian đáp ứng nhỏ, hệ thống làm việc ổn định.
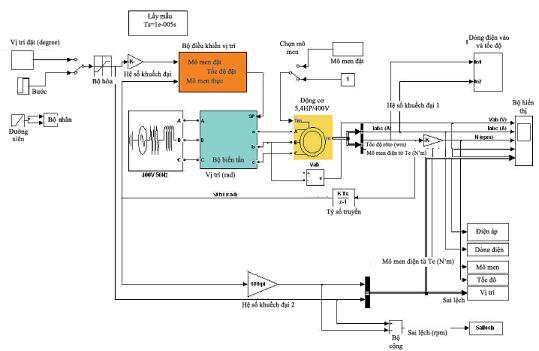
Hình 9: Mô hình mô phỏng hệ truyền động bám vị trí điều khiển động cơ không đồng bộ roto lồng sóc.
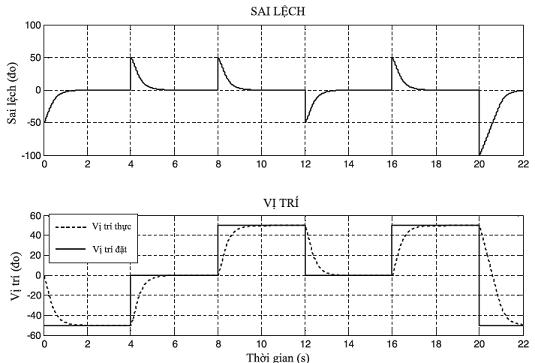
Hình 10: Kết quả mô phỏng bám theo vị trí và độ sai lệch của hệ truyền động bám xoay chiều.
b. Quá trình điều khiển trong thực tế
Trong hệ thống điều khiển trước kia, điều khiển được thực hiện thông qua các cổng logic cơ bản: kết hợp IC số với các bộ cảm biến. Các linh kiện nối cứng với nhau nên khi thay đổi thuật toán điều khiển thì phải thực hiện đấu nối lại. Trong những thập niên gần đây, sự phát triển của thiết bị PLC đã giải quyết được những hạn chế trên. Dùng PLC điều khiển hệ biến tần - động cơ bằng các lệnh lập trình linh hoạt theo yêu cầu của bài toán, phương pháp điều khiển mềm thay đổi thông qua PLC mà không phải thay đổi cấu trúc phần cứng.
Trong hệ điều khiển trên, máy tính vừa thực hiện điều khiển và giám sát quá trình điều khiển thông qua PLC, PLC điều khiển hệ biến tần - động cơ bằng cách lệnh lập trình, đây là phương pháp điều khiển mềm bằng cách lập trình thay đổi thông qua PLC mà không phải thay đổi phần cứng (đấu nối rơ le...).
Để giám sát dòng điện, nhiệt độ, điện áp, công suất hoặc đặt lại tốc độ của động cơ thì cần thiết phải kết nối biến tần với PLC, các lệnh được lập trình trên máy tính. Các tín hiệu phản hồi được thực hiện nhờ các thiết bị sensor, bộ cảm biến nhiệt độ…Do đặc thù các PLC đặt tại hiện trường, khoảng cách truyền dẫn xa, tốc độ truyền lớn, nhiều PLC kết nối với một máy tính nên chọn giao tiếp giữa máy tính và PLC qua cổng giao tiếp RS485. Giao tiếp PLC và biến tần thông qua giao thức Profibus DP. PLC thu thập các tín hiệu về tốc độ, vị trí. Các khối PID tích hợp trong PLC hoặc modul PID mở rộng bên ngoài thực hiện tính toán, từ đó điều chỉnh các tham số đó và đưa ra tín hiệu điều khiển biến tần.
Hình 11: Sơ đồ thực nghiệm hệ điều khiển bám.
Trong nhà máy xi măng, làm thế nào để phối liệu clinker, thạch cao, phụ gia theo tỷ lệ tương ứng để nghiền thành xi măng? Làm thế nào để định lượng đưa vào máy nghiền tổng khối lượng không thay đổi trong khi đó ngoài khối lượng định lượng clinker, thạch cao, phụ gia đầu vào còn có liệu hồi về ở đầu ra của máy nghiền (đó là những hạt có khối lượng lớn không phân ly động được)? Lượng hiện đang tồn trong máy nghiền (Nghiền bi), hệ thống cân băng định lượng cần phối trộn các chất theo tỷ lệ định trước, nguyên lý làm việc của hệ thống này dựa trên quá trình điều chỉnh tự động tỷ lệ từng thành phần tương ứng với tỷ lệ đặt trước dựa trên cơ sở các vòng lặp điều chỉnh PI, PID.
Chúng ta cũng có thể bắt gặp ứng dụng bộ điều chỉnh PID trong quá trình làm lạnh clinker. Khí làm mát được thổi vào khoang dưới ghi làm lạnh clinker. Clinker được làm lạnh bằng phương pháp này và thu hồi lượng nhiệt từ clinker. Áp suất khoang dưới của ghi làm lạnh được giám sát và được lấy trực tiếp theo tỷ lệ dàn đều trên ghi làm lạnh. Ở điều kiện tối đa, số lượng ckinker đưa vào tăng được dải đều trên ghi làm lạnh làm cho áp lực khoang dưới tăng. Bộ đáp ứng điều khiển sẽ điều chỉnh các tham số và thực hiện tăng tốc độ của ghi làm lạnh để vận chuyển clinker ra khỏi lò.
Trong quá trình ngược lại, khi lượng clinker đưa vào giảm, lớp clinker mỏng ra và áp lực khoang dưới giảm. Đáp ứng điều khiển sẽ thực hiện điều chỉnh làm chậm ghi làm lạnh đi và giữ clinker trên ghi lò lâu hơn để tăng dần độ cao lớp clinker. Tất cả những quá trình điều khiển này được miêu tả theo sơ đồ (Hình 12).
Hình 12: Sơ đồ nguyên lý bộ điều chỉnh PID ghi làm lạnh
Kết luận: Như vậy, thông qua bài viết này, chúng ta đã phần nào trả lời được hai câu hỏi nêu ở trên. Đồng thời chúng ta có thể hiểu được bản chất của hệ thống điều khiển truyền động PLC - biến tần - động cơ, quá trình làm việc tự động hóa và ứng dụng hệ thống này trong các công đoạn sản xuất của nhà máy xi măng.
2. Điều chỉnh ổn định tốc độ động cơ của PLC
Trong phần này, chúng ta sẽ tìm hiểu quá trình điều khiển bám theo vị trí và tốc độ động cơ của hệ truyền động PLC - Biến tần - động cơ.
PID là bộ điều khiển kín được coi là lý tưởng đối với các tham số các bộ điều khiển liên tục. Kết hợp giữa các bộ điều khiển tỷ lệ - tích phân - vi phân, PID được coi là bộ điều khiển động mà việc thay đổi tham số của bộ điều khiển có khả năng làm thay đổi các đặc tính động và đặc tính tĩnh của hệ điều khiển tự động.
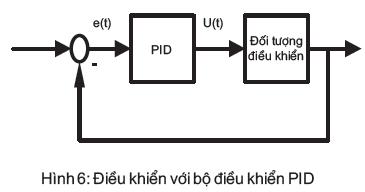
Hình 6: Điều khiển với bộ điều khiển PID
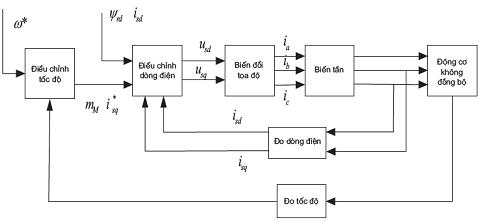
Hình 7: Các vòng điều khiển trong hệ truyền động điện
Đặc biệt trong hệ điều khiển PLC - biến tần - động cơ, để thấy rõ được vai trò của bộ điều khiển PID trong quá trình điều khiển ổn định tốc độ và vị trí góc của hệ này, dựa trên những thông tin phần trên, ta tiến hành xây dựng mô hình điều khiển dựa trên công cụ có sẵn Matlab. Theo sơ đồ cấu trúc hình thu thập giá trị đặc tính bám của hệ thống trước và sau khi có bộ điều chỉnh PID.
Từ đó, ta có mô hình bài toán điều khiển bám động cơ không đồng bộ ba pha theo phương pháp tựa theo từ thông roto:
a. Xây dựng mô hình điều khiển bám trong Matlab
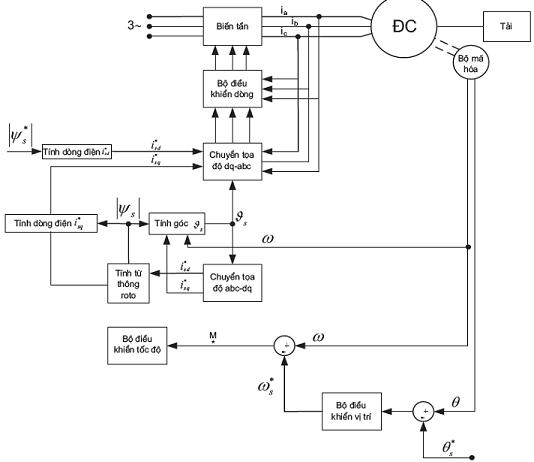
Hình 8: Mô hình điều khiển động cơ không đồng bộ định hướng từ thông roto
Các khối có sẵn ta lần lượt xây dựng các khối điều khiển: vị trí, biến tần, khối nguồn trong thư viện của Matlab. Hệ thống thực hiện vòng điều chỉnh phản hồi: dòng điện, mô men, tốc độ, vị trí.
Quá trình điều khiển như sau:
Khi có tốc độ chuẩn từ khối điều khiển vị trí đưa vào, tốc độ của động cơ được tính toán qua khối tính dòng i*sq, tốc độ thực tế của động cơ đo được đưa đến bộ điều chỉnh tốc độ, bộ tính toán từ thông được chuyển đổi thành các dòng điều khiển theo trục dq và trục αβ đưa đến bộ điều chỉnh dòng vào đưa ra tín hiệu xung điều khiển đóng mở bộ nghịch lưu có điều khiển trong khối biến tần. Thực tế, các khối điều khiển tốc độ, vị trí góc được xây dựng từ các hàm tỷ lệ - tích phân - vi phân dựa trên sơ đồ cấu trúc trên.
Thực hiện mô phỏng và điều chỉnh các tham số bộ PID ta có kết quả như sau với thời gian đáp ứng nhỏ, hệ thống làm việc ổn định.
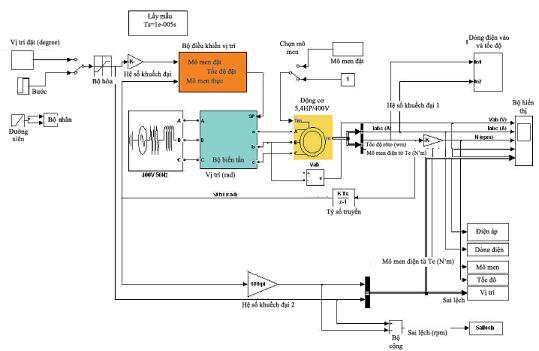
Hình 9: Mô hình mô phỏng hệ truyền động bám vị trí điều khiển động cơ không đồng bộ roto lồng sóc.
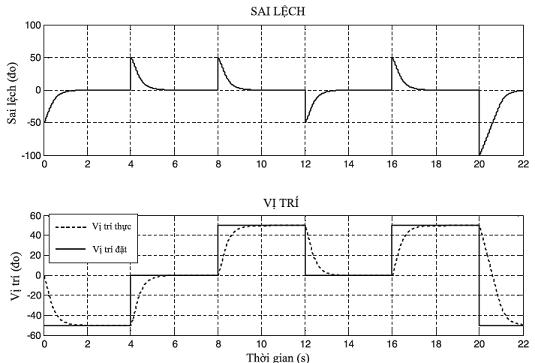
Hình 10: Kết quả mô phỏng bám theo vị trí và độ sai lệch của hệ truyền động bám xoay chiều.
b. Quá trình điều khiển trong thực tế
Trong hệ thống điều khiển trước kia, điều khiển được thực hiện thông qua các cổng logic cơ bản: kết hợp IC số với các bộ cảm biến. Các linh kiện nối cứng với nhau nên khi thay đổi thuật toán điều khiển thì phải thực hiện đấu nối lại. Trong những thập niên gần đây, sự phát triển của thiết bị PLC đã giải quyết được những hạn chế trên. Dùng PLC điều khiển hệ biến tần - động cơ bằng các lệnh lập trình linh hoạt theo yêu cầu của bài toán, phương pháp điều khiển mềm thay đổi thông qua PLC mà không phải thay đổi cấu trúc phần cứng.
Trong hệ điều khiển trên, máy tính vừa thực hiện điều khiển và giám sát quá trình điều khiển thông qua PLC, PLC điều khiển hệ biến tần - động cơ bằng cách lệnh lập trình, đây là phương pháp điều khiển mềm bằng cách lập trình thay đổi thông qua PLC mà không phải thay đổi phần cứng (đấu nối rơ le...).
Để giám sát dòng điện, nhiệt độ, điện áp, công suất hoặc đặt lại tốc độ của động cơ thì cần thiết phải kết nối biến tần với PLC, các lệnh được lập trình trên máy tính. Các tín hiệu phản hồi được thực hiện nhờ các thiết bị sensor, bộ cảm biến nhiệt độ…Do đặc thù các PLC đặt tại hiện trường, khoảng cách truyền dẫn xa, tốc độ truyền lớn, nhiều PLC kết nối với một máy tính nên chọn giao tiếp giữa máy tính và PLC qua cổng giao tiếp RS485. Giao tiếp PLC và biến tần thông qua giao thức Profibus DP. PLC thu thập các tín hiệu về tốc độ, vị trí. Các khối PID tích hợp trong PLC hoặc modul PID mở rộng bên ngoài thực hiện tính toán, từ đó điều chỉnh các tham số đó và đưa ra tín hiệu điều khiển biến tần.
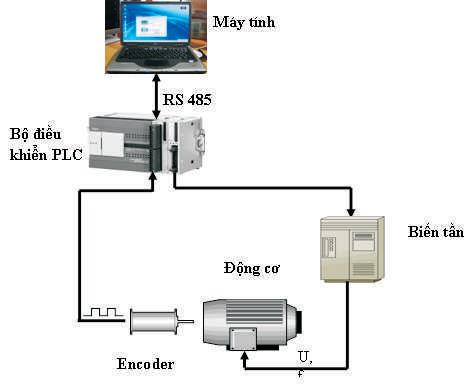
Hình 11: Sơ đồ thực nghiệm hệ điều khiển bám.
Trong nhà máy xi măng, làm thế nào để phối liệu clinker, thạch cao, phụ gia theo tỷ lệ tương ứng để nghiền thành xi măng? Làm thế nào để định lượng đưa vào máy nghiền tổng khối lượng không thay đổi trong khi đó ngoài khối lượng định lượng clinker, thạch cao, phụ gia đầu vào còn có liệu hồi về ở đầu ra của máy nghiền (đó là những hạt có khối lượng lớn không phân ly động được)? Lượng hiện đang tồn trong máy nghiền (Nghiền bi), hệ thống cân băng định lượng cần phối trộn các chất theo tỷ lệ định trước, nguyên lý làm việc của hệ thống này dựa trên quá trình điều chỉnh tự động tỷ lệ từng thành phần tương ứng với tỷ lệ đặt trước dựa trên cơ sở các vòng lặp điều chỉnh PI, PID.
Chúng ta cũng có thể bắt gặp ứng dụng bộ điều chỉnh PID trong quá trình làm lạnh clinker. Khí làm mát được thổi vào khoang dưới ghi làm lạnh clinker. Clinker được làm lạnh bằng phương pháp này và thu hồi lượng nhiệt từ clinker. Áp suất khoang dưới của ghi làm lạnh được giám sát và được lấy trực tiếp theo tỷ lệ dàn đều trên ghi làm lạnh. Ở điều kiện tối đa, số lượng ckinker đưa vào tăng được dải đều trên ghi làm lạnh làm cho áp lực khoang dưới tăng. Bộ đáp ứng điều khiển sẽ điều chỉnh các tham số và thực hiện tăng tốc độ của ghi làm lạnh để vận chuyển clinker ra khỏi lò.
Trong quá trình ngược lại, khi lượng clinker đưa vào giảm, lớp clinker mỏng ra và áp lực khoang dưới giảm. Đáp ứng điều khiển sẽ thực hiện điều chỉnh làm chậm ghi làm lạnh đi và giữ clinker trên ghi lò lâu hơn để tăng dần độ cao lớp clinker. Tất cả những quá trình điều khiển này được miêu tả theo sơ đồ (Hình 12).
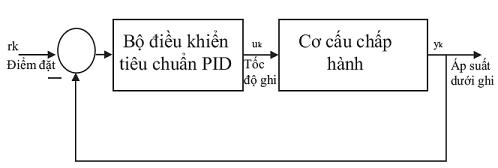
Hình 12: Sơ đồ nguyên lý bộ điều chỉnh PID ghi làm lạnh
Kết luận: Như vậy, thông qua bài viết này, chúng ta đã phần nào trả lời được hai câu hỏi nêu ở trên. Đồng thời chúng ta có thể hiểu được bản chất của hệ thống điều khiển truyền động PLC - biến tần - động cơ, quá trình làm việc tự động hóa và ứng dụng hệ thống này trong các công đoạn sản xuất của nhà máy xi măng.
ximang.vn * (Nguồn: Tạp chí Thông tin KHCN-Vicem)