Giải đáp thêm các câu hỏi tại Hội thảo kỹ thuật xi măng ACT - 2024
» Sau khi diễn ra Hội thảo kỹ thuật ACT 2024 "Những tiến bộ công nghệ trong sản xuất xi măng" với chủ đề “Giải pháp tiết kiệm năng lượng và giảm phát thải trong sản xuất xi măng”, Ban Tổ chức đã nhận được nhiều câu hỏi từ các nhà máy, viện nghiên cứu về các chủ đề đã trình bày tại Hội thảo. Thay mặt BTC, chúng tôi xin cảm ơn sự quan tâm của các bạn về các nội dung đang khá nóng hiện nay.
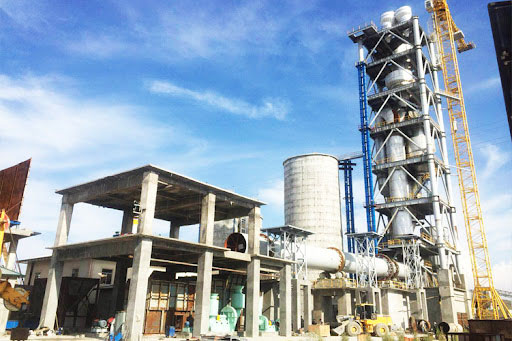
Sau khi thảo luận với diễn giả (Công ty C-HOPE Nam Kinh), BTC ACT-2024 xin cung cấp thêm một số thông tin liên quan đến việc áp dụng tiến bộ kỹ thuật - công nghệ để tiết kiệm năng lượng, giảm phát thải tại các nhà máy xi măng hiện nay.
Câu hỏi 1: Tỷ lệ đốt rác thải thay thế của loại buồng đốt trước này trên lò calciner cho từng loại lò nung khác nhau là bao nhiêu phần trăm (20 - 40%)? Tỷ lệ này có bị ảnh hưởng bởi công suất lò nung? Cho ví dụ cụ thể với từng loại lò nung công suất khác nhau như: 3.000 tpd, 6.000 tpd, 8.000 tpd, 10.000 tpd…
C-HOPE: Thông thường tỉ lệ sử dụng rác thải làm nhiên liệu thay thế trong lò calciner là 20 - 80%. Tỷ lệ thay thế chủ yếu do các yếu tố như kích thước, độ ẩm, nhiệt trị, hàm lượng nguyên tố có hại trong nhiên liệu thay thế, thể tích lò calciner, có buồng đốt trước hay không quyết định, cơ bản không chịu ảnh hưởng bởi công suất lò nung.
Câu hỏi 2: Suất đầu tư trung bình cho buồng đốt ngoài đối với các loại lò nung nêu trên là bao nhiêu? Chi phí đầu tư tính theo tấn xi măng hay tấn rác đốt?
C-HOPE: Chi phí đầu tư cho buồng đốt trước chủ yếu quyết định bởi quy cách, vật liệu chịu lửa kèm theo và không gian khung tháp trao đổi nhiệt đuôi lò nung. Thông số này thường được tính theo tấn rác đốt (quy tiêu chuẩn) hoặc tỷ lệ thay thế nhiên liệu (tiêu chuẩn). Tuy nhiên, việc này chưa được chuẩn hóa nên khó xác định một mức trung bình.
Câu hỏi 3: Lượng gió 3 đưa vào buồng đốt là bao nhiêu?
CHOPE: Thông thường, lượng gió 3 mà buồng đốt trước sử dụng chiếm tỷ lệ khoảng 30 - 40%. Khi tỷ lệ nhiên liệu thay thế tăng cao, lượng gió 3 cần sử dụng cũng sẽ tăng theo.
Câu hỏi 4: Làm thế nào để lấy dị vật lẫn trong nguyên liệu thay thế ra khỏi buồng đốt?
CHOPE: Thông thường, dị vật lẫn trong nguyên liệu thay thế cơ bản đã được loại bỏ ở công đoạn tiền xử lý. Nếu như nhiên liệu thay thế có chứa dị vật không cháy hết đi vào buồng đốt trước, các tạp chất nặng sau khi được gia nhiệt sơ bộ trong buồng đốt trước mới đi vào lò calciner và lò quay. Thông thường, buồng đốt trước không cần lắp đặt thêm thiết bị lấy dị vật ra khỏi buồng.
Câu hỏi 5: Làm thế nào để kiểm soát cháy trong buồng đốt nếu không may nguyên liệu thay thế có lẫn các chất phát sinh nhiệt lớn (lẫn chai xăng chẳng hạn)?
CHOPE: Nếu như trong nguyên liệu thay thế có lẫn các chất phát sinh nhiệt lớn (như chai xăng), sẽ dẫn đến nhiệt độ đầu ra của buồng đốt trước quá cao, cần phải áp dụng các thao tác sau:
1. Chia một lượng nhỏ bột liệu đi vào buồng đốt trước
2. Gia tăng tần suất đẩy của tấm đẩy thủy lực, tần suất phun thổi của cannon bắn khí, giảm thiểu thời gian vật liệu lưu lại trong buồng đốt trước nhằm vật liệu bên trong buồng đốt trước có thể nhanh chóng di chuyển từ đoạn đầu vào cấp liệu xuống đoạn đầu ra
3. Kiểm soát lượng gió 3 đi vào buồng đốt trước.
Câu hỏi 6: Đề nghị cấp catalogue thông số kỹ thuật của buồng đốt?
CHOPE: Đây là một số thông tin cơ bản:
Hình ngoài thiết bị | ![]() |
Năng suất xử lý | ≥20 t/h |
Thanh đẩy thủy lực | 2 hàng |
Nhóm canon bắn khí | 6 hàng 12 bậc |
Kích thước ngoài thiết bị, (m) (dài×rộng×cao) |
~9,5×4,3×8,4(H) |
Thể tích sử dụng, (m³) | ~55 |
Thời gian lưu lại, (m³) | 5~20 |
Lượng khí nén sử dụng | 17 Nm³/min (0,4~0,6 MPa) |
Công suất lắp máy | ~40kW |
Câu hỏi 7: Cho biết hiệu quả kinh tế kỹ thuật của tháp trao đổi nhiệt 6 cấp cyclon so với tháp trao đổi nhiệt 5 cấp cyclon (chỉ phí xây dựng, chi phí tiêu thụ điện, tiêu thụ than...)
CHOPE: Lấy dự án xây mới với công suất 5.000 tpd làm ví dụ, chi phí xây dựng tháp trao đổi nhiệt 6 cấp tăng thêm khoảng 1,1 triệu USD so với tháp trao đổi nhiệt 5 cấp. Nhiệt độ đầu ra C1 của tháp trao đổi nhiệt 6 cấp thấp hơn khoảng 50°C so với tháp 5 cấp, tiêu hao nhiệt clinker giảm khoảng 25 kCal/kg clinker. Giả sử giá than thô tính theo 100 USD/tấn, số ngày sản xuất trên một năm là 300 ngày, thì lợi nhuận năm của nhà máy bởi giảm tiêu hao than sẽ được tăng 720.000 USD, như vậy chỉ sau khoảng 1,5 năm là sẽ thu hồi vốn, trở lực của tháp trao đổi nhiệt 6 cấp theo thiết kế trở lực siêu thấp gần bằng với tháp trao đổi nhiệt 5 cấp, do đó tiêu hao điện không tăng.
Câu hỏi 8: Khí thải ra khỏi tháp trao đội nhiệt 6 cấp cyclon có nhiệt độ thấp (khoảng 290°C) không đủ sấy nghiền liệu thì giai quyết bằng biện pháp công nghệ nào?
CHOPE: Nhiệt độ đầu ra tháp trao đổi nhiệt 6 cấp là 260°C~280°C, độ ẩm tổng hợp của nguyên liệu vào mùa khô ở Việt Nam là 3~3,5%, nhiệt độ gió nóng đi vào máy nghiền cần là 190°C~200°C; Khi độ ẩm tổng hợp của nguyên liệu vào mùa mưa ở Việt Nam là 5~5,5%, nhiệt độ gió nóng vào máy nghiền cần là 240°C ~250°C, do vậy nhiệt độ đầu ra khí thải tháp trao đổi nhiệt 6 cấp vẫn đáp ứng phần lớn yêu cầu. Do một số nguyên nhân đặc thù, thỉnh thoảng độ ẩm tổng hợp của nguyên liệu ≥ 6%, thì có thể áp dụng phương án thiết kế chuyển đổi giữa tháp 5 cấp và 6 cấp, khi cần nhiệt độ gió nóng cao thì chuyển sang sử dụng tháp trao đổi nhiệt 5 cấp, nếu độ ẩm tổng hợp của nguyên liệu thường xuyên ≥ 6% thì không nên sử dụng tháp trao đổi nhiệt 6 cấp mà sử dụng tháp trao đổi nhiệt 5 cấp.
Câu hỏi 9: Hiện tại cứ 1 tấn clinker, phát thải 0,81 tấn CO₂, như vậy nếu sản xuất 3 tỷ tấn clinker thì sẽ phát thải khoảng 2.43 tỷ tấn CO₂ làm biến đổi khí hậu. Xin cho có phương án công nghệ mới nào trong nung luyện clinker để giảm phát thải CO₂ không?
CHOPE: Điều này khó có thể nói hết ý trong một bài ngắn.
Các dây chuyền sản xuất xây mới đang áp dụng kỹ thuật công nghệ tiết kiệm năng lượng 2.0 mới nhất, đối với các dây chuyền sản xuất hiện có, sau khi thông qua việc cải tạo kỹ thuật tiết kiệm năng lượng đều được thực hiện giảm tiêu hao nhiệt clinker, từ đó giảm thiểu CO₂ sản sinh trong quá trinh đốt than.
Có rất nhiều rác thải sinh hoạt, rác thải nông nghiệp và rác thải công nghiệp có nhiệt trị cao, và cần tiến hành xử lý đốt cháy vô hại hóa thì được làm nhiên liệu thay thế và đưa vào lò calciner, nhờ đó sẽ giảm thiểu lượng CO₂ sản sinh trong quá trình đốt than.
Sử dụng vật liệu có hàm lượng canxi cao carbon thấp để thay thế đá vôi hoặc đất sét nung như xỉ lò đất đèn, giảm thiểu lượng CO₂ sản sinh trong quá trình nguyên liệu phân giải.
Câu hỏi 10: Trước năm 1997 hệ thống nghiền xi măng tại Việt Nam chủ yếu sử dụng nghiền bi, đến năm 1998 sử dụng đan xen hệ thống nghiền đứng sơ bộ và nghiền bi. Cho đến năm 2010, sử dụng hệ thống nghiền đứng, đến năm 2014 sử dụng hệ thống cán ép và nghiền bi. Hiện tại, CHOPE đã giới thiệu hệ thống nghiền đứng sơ bộ và nghiền bi để nghiền xi măng (giống nhà máy Xi măng Bút Sơn đã có từ 1998). So sánh hiệu quả kinh tế kỹ thuật của hệ thống nghiền đứng với hệ thống nghiền đứng sơ bộ và nghiền bi trong quá trình nghiền xi măng?
CHOPE: Nghiền đứng để nghiền xi xi măng có những ưu điểm là lưu trình công nghệ đơn giản, thiết bị ít, quản lý thuận tiện, tuy nhiên xi măng thành phẩm được nghiền từ máy nghiền đứng do hình dạng hạt tương đối phẳng dẹt, lượng nước tiêu chuẩn của xi măng cao, đối với khách hàng có yêu cầu nhạy cảm về lượng nước tiêu chuẩn của xi măng sẽ không chấp nhận sản phẩm xi măng nghiền bằng máy nghiền đứng, nên ảnh hưởng đến việc tiêu thụ sản phẩm. Hơn nữa, nghiền đứng làm nghiền xi thành phẩm cuối cùng cần lắp đặt buồng đốt phụ gió nóng hoặc dùng khí nóng từ lò nung để làm nguồn nhiệt sấy khô.
Hệ thống nghiền đứng làm tiền nghiền và nghiền bi, đa số xi măng được nghiền bằng máy nghiền bi, hạt xi măng có độ tròn tốt, tính lưu động của xi măng tốt, lượng nước tiêu chuẩn của xi măng thấp, khách hàng có yêu cầu nhạy cảm về lượng nước tiêu chuẩn của xi măng cũng dễ chấp nhận, thị trường tiêu thụ tốt, hơn nữa không cần lắp đặt thêm buồng đốt phụ cấp gió nóng.
Hệ thống nghiền đứng làm tiền nghiền và nghiền bi do CHOPE thiết kế gần giống với hệ thống nghiền xi măng của nhà máy Xi măng Bút Sơn, tuy nhiên cũng có những điểm khác nhau, chủ yếu là: quy cách của máy nghiền đứng làm tiền nghiền lớn hơn, cùng với máy phân ly hình chữ V và máy tiền phân ly là hệ thống phân ly 3 cấp loại mới nhất, hiệu quả phân ly cao, chia thành 3 cấp độ, hạt có kích thước thô và cỡ vừa được quay về máy nghiền đứng, hạt có kích thước mịn đi vào máy nghiền bi, hạt có kích thước siêu mịn được chọn lọc ra làm thành phẩm, do vậy hệ thống có các ưu điểm như sản lượng cao, tiêu hao điện thấp, hơn nữa khả năng thích ứng với nguyên liệu mạnh mẽ. Nghiền đứng tiền nghiền áp dụng thao tác áp suất thấp, số lần hàn đắp ít, tỉ suất vận hành cao, chi phí bảo trì thiết bị thấp.
Câu hỏi 11: Hệ thống bypass thoát clo, kiềm, SOx chi phí khoảng bao nhiêu USD và tổn thất nhiệt khoảng bao nhiêu kCal/kg clinker? Có thể mất đến 5 triệu USD và tổn thất từ 5 - 7 kCal/kg clinker?
CHOPE: Cần căn cứ vào hàm lượng S, Cl-, SOx để xác định lượng gió trích, lấy dây chuyền sản xuất công suất 5.000 tpd, và lượng gió bypass trích khoảng 2~5% (2~5% của lượng gió buồng khói) làm ví dụ, tiêu hao nhiệt khoảng 5 - 10 kCal/kg clinker như vậy chi phí đầu tư khoảng 2,2 ~2,5 triệu USD.
Chi phí đầu tư hệ thống bypass có liên quan đến quy cách lò nung, tỷ lệ lượng gió trích ra và việc có thể bố trí lắp đặt được các thiết bị như máy làm lạnh gió, máy lọc bụi túi và quạt gió... trong khung tháp trao đổi nhiệt hay không, phương án kỹ thuật được xác định căn cứ vào tình hình thực tế của mỗi nhà máy. Cứ mỗi 1% gió trích ra thì tương đương tiêu hao nhiệt của clinker sẽ tăng thêm 2 kCal/kg clinker.
BTC ACT-2024