Giảm thiểu phát thải, gia tăng sử dụng tối đa nhiên liệu thay thế (P2)
Trong bài viết này, Tiến sỹ Stefan Kern, A TEC Production and Services GmbH, trình bày chi tiết dự án chuyển đổi lò nung tại Lafarge Retznei và cách thức mà thiết kế calciner được tối ưu hóa cho phép sử dụng 100% nhiên liệu thay thế ra sao.
>> Giảm thiểu phát thải, gia tăng sử dụng tối đa nhiên liệu thay thế (P1)
Để đạt được các mục tiêu này, các tiến trình thực hiện dưới đây đã được áp dụng:
1. Calciner nội tuyến mới đã không thể đặt được vào bên trong tòa nhà công trình hiện có; do đó, nó đã được đặt ở phía trước tháp sấy sơ bộ hiện có trong một kết cấu thép mới (Hình 3).
Thách thức là, như trong rất nhiều hệ thống calciner được trang bị thêm, phải đạt được tất cả các độ nghiêng cho các góc và các mặt cắt nhỏ đã biết nhằm đảm bảo các điều kiện vận hành phù hợp và giảm thiểu hồi lưu bột liệu và tích tụ liệu ở những khu vực đã biết.
Vì hệ thống sấy sơ bộ là một hệ thống hai nhánh nên đã quyết định rằng đầu trên calciner sẽ được thiết kế như một calciner thông thường, được chia nhánh tại đỉnh ở buồng đốt sau (PCC) A TEC thành hai ống dẫn xuống dưới đối xứng nhau, mỗi ống đi vào một trong hai cyclone tầng đáy.
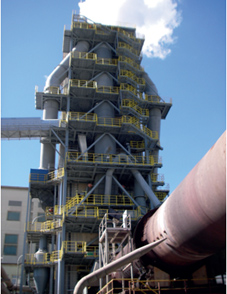
Hình 5. Calciner nội tuyến mới đã hoàn thành tại Retznei.
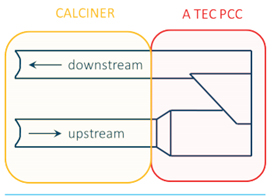
Hình 6. Sơ đồ Buồng Đốt Sau của A TEC (PCC).
Để có thể đấu nối calciner mới với lò nung ở phía đầu vào và với sấy sơ bộ ở phía đầu ra, các điểm đấu nối ở sấy sơ bộ đã được thiết kế lại hoàn toàn. Các cyclone tầng đáy là hai cyclone được thiết kế mới, có đường kính lớn hơn để tăng hiệu suất quá trình lên do dòng khí có thể cao hơn được tạo ra do gia tăng sử dụng SSW sau khi điều chỉnh. Hơn nữa, các đầu vào được xoay 90° và hai nhánh calciner phía dưới đi vào hai cyclone tầng đáy từ bên trái và bên phải tháp sấy sơ bộ thay vì từ phía trước để đảm bảo độ dốc các góc và tránh được các đầu vào cyclone phẳng.
Để đấu nối calciner với lò nung, lò nung đã được cắt ngắn đi khoảng 3m. Điều này cho phép di chuyển buồng đầu vào lò nung về phía trước tòa nhà sấy sơ bộ và tạo được độ dốc nghiêng cho phần đấu nối của calciner với phần vòi phun.
Toàn cảnh calciner sau khi điều chỉnh có thể thấy ở Hình 5.
2. Các đầu vào nhiên liệu của ba loại nhiên liệu (dung môi, than cốc/than và SSW) đã được bố trí tại khu vực đầu vào gió ba thấp hơn để bắt cháy thuận lợi. Đầu vào gió ba thứ hai đã được bố trí cao hơn ở phần phía trên của calciner. Ở khu vực này, vùng khử giảm được hình thành, mà phía sau đầu vào gió ba thứ hai được oxi hóa nhưng vẫn hoạt động phần nào trong vài giây. Để đốt cháy hết một cách an toàn bất kỳ nhiên liệu nào chưa cháy và CO, xuất phát từ vùng khử giảm NOx, thời gian lưu khí vừa đủ trong calciner là cần thiết. Thiết kế calciner được lựa chọn ở đây cho thấy một tính năng mà tránh được việc cần đến các calciner rất lớn, và mang lại kết quả mà có thể đạt được với thời gian lưu thực tế hợp lý. Tính năng này được gọi là Buồng Đốt Sau (PCC).5 Thiết kế của PCC cho thấy những đặc điểm sau: Ở dòng hướng lên của PCC, đường kính được nâng lên để tăng thêm thời gian lưu cho các hạt mà chưa hoàn toàn cháy hết (Hình 6). Đầu vào phần phía dưới calciner được thiết kế lệch tâm để tạo ra sự rối loạn và hiệu quả phối trộn như đã chỉ ra ở mô hình dòng chảy trong Hình 7. Nhìn từ trên xuống PCC ở nhà máy Retznei được thể hiện ở Hình 8. Điều này mang lại hiệu quả là vật chất chưa cháy và các khí (CO...) được phối trộn hiệu quả với khí đốt chưa dùng hết và hoàn thành việc đốt cháy chúng trước khi đi vào các cyclone sấy sơ bộ. Tổng thời gian lưu khí thiết lập trong calciner là 5,9 giây, thấp hơn nhiều so với các hệ thống thông thường để đạt được các thông số hiệu suất yêu cầu về đốt cháy hết và khử giảm NOx.
3. Nhánh phụ Cl hiện có đã được thiết kế ban đầu cho tỷ lệ nhánh phụ là 5% khi đưa vào vận hành cho lò nung có thiết bị sấy sơ bộ. Nhánh phụ này đã được nâng cấp cải tạo nhằm đạt được tỷ lệ nhánh phụ xấp xỉ 10% để có thể xử lý Cl đầu vào tăng lên do tỷ lệ SSW cao hơn. Vì khí đốt riêng cho lò ở đầu vào lò nung gần bằng một nửa lượng khí đốt cho vận hành calciner so với vận hành sấy sơ bộ, có thể tăng lượng khí đốt này lên bằng cách lắp một chụp rẽ nhánh thích hợp và một tầng làm nguội mới. Lọc bụi và quạt bypass hiện có có thể sử dụng như một lượng khí đốt tuyệt đối gần giống như trước khi điều chỉnh.
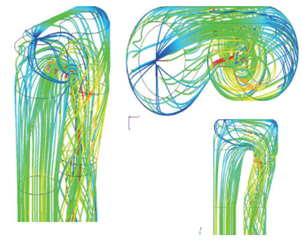
Hình 7. Mô hình dòng chạy được lập theo CFD trong PCC.
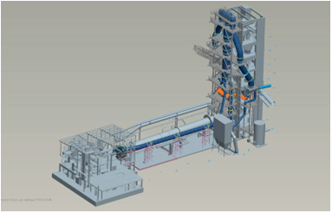
Hình 8. Nhìn từ trên xuốn dưới calciner (PCC) ở Retznei.
4. Hệ thống nhiên liệu cho SSW đã đặt ra thách thức không chỉ đối với việc định lượng nguyên liệu ổn định cho hệ thống, mà còn vận chuyển nó từ cơ sở chuẩn bị của Thermoteam nằm cách đó gần 250 m. A TEC đã lựa chọn băng tải chữ U để thực hiện công việc này. Băng tải này tương tự như băng tải ống, nhưng phần băng tải mà trong đó liệu được vận chuyển là phần được mở ra ở trên cùng (băng tải được uốn cong thành hình chữ U) và được đậy nắp riêng để tránh tràn liệu. Băng tải quay về được đậy kín hoàn toàn để tránh tràn liệu. Băng tải được đậy kín từng phần mang lại những lợi ích vận hành vì nó không nhạy cảm với nguyên liệu quá cỡ mà nếu không sẽ gây thủng băng. Hình 9 chỉ ra một phần băng tải chữ U và Hình 10 cho thấy các két định lượng tới băng tải.
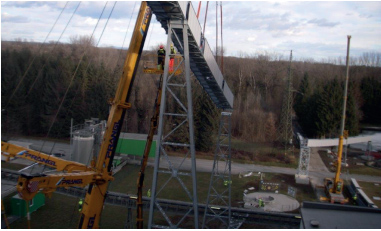
Hình 9. Lắp đặt băng tải cho SSW từ hạng mục công trình Thermoteam (cơ sở chuẩn bị) tới điểm cấp liệu calciner.
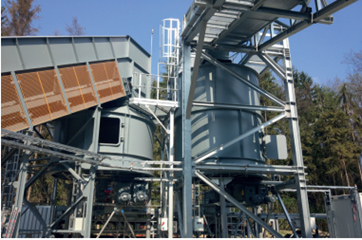
Hình 10. Các két định lượng cho SSW tới băng tải.
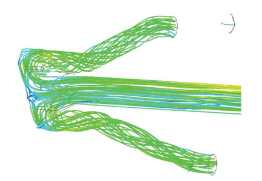
Hình 11. Lập mô hình hình học CFD (các dòng chảy - màu sắc biểu đạt vận tốc).
Đo lường nguyên liệu được thực hiện tại đầu vào băng tải chữ U bởi một két chứa phía trước có thiết bị khuấy trên tế bào tải. Băng tải chữ U có thể được chất tải đồng thời từ thiết bị Thermoteam hoặc từ trạm dỡ tải lên xe tải mới để đạt được sự linh hoạt cao nhất.
5. Một hệ thống mới hoàn toàn, tùy biến đã được lắp đặt để vận chuyển và định lượng các nhiên liệu thay thế dạng lỏng (LAF, dung môi). Vì một trong những điều kiện biên đó là có thể xuất hiện các hạt có kích thước lên đến 5mm, một hệ thống đặc biệt đã được thiết kế trong đó tốc độ dòng thể tích được kiểm soát hoàn toàn nhờ một máy bơm kiểu pittong điều tốc, tránh tạo áp cho bất kỳ thiết bị nào trong hệ thống dẫn tới vòi phun. Riêng đối với vòi phun, cái gọi là ‘vòi phun buồng hở’ đã được sử dụng để phun chất lỏng bằng khí nén; kết quả là có thể nhìn thấy lỗ mở vòi phun lớn.
6. Hệ thống SNCR là một tiêu điểm của quá trình riêng biệt. Như đã trình bày ở trên, hệ thống sẽ phải được thiết kế sao cho đạt được hiệu suất tối đa nhưng cũng phải lắp được vào trong calciner để cho phép:
- Giảm thiểu ảnh hưởng tới quá trình khử giảm NOx sơ cấp thông qua việc đốt cháy từng bậc và chỉ xử lý những lượng NOx sót lại sau khi đốt từng bậc.
- Xử lý được cả lượng thấp (SSW/LAF hoạt động) lẫn lượng cao (than cốc) NOx cơ sở.
- Đạt được độ trượt ammonia thấp.
Khái niệm được lựa chọn là để phun vào phần phía dưới của calciner theo hai cấp độ. Cấp độ thứ nhất là ngay phía trước đầu vào mỗi cyclone tầng 4, cấp độ thứ hai là đầu vào cấp độ thứ nhất nói trên. Trong quá trình vận hành đốt bằng than cốc cho calciner, cấp độ thứ hai của vòi phun có thể được kích hoạt.
Thiết kế hoàn chỉnh calciner, bao gồm cả định vị vòi phun, đã được kiểm tra thông qua phân tích CFD để xác thực các kết quả tính toán (Hình 11)
A TEC Production and Services GmbH là nhà thầu thi công chính cho dự án trên cơ sở EPC cơ khí. Công ty đã chịu trách nhiệm về thiết kế hoàn chỉnh, tháo dỡ, gia công chế tạo và lắp đặt kết cấu thép và thiết bị bao gồm cả các công việc và các dịch vụ cần thiết tại hiện trường thi công.
Các công tác thi công lắp dựng cơ khí tại hiện trường nhà máy Retznei đã bắt đầu thực hiện vào cuối mùa hè năm 2018 với việc lắp dựng kết cấu thép cho caclciner mới tiếp theo là lắp đặt calciner. Cả hai công việc đều đã được hoàn thành trong tháng 12/2018.
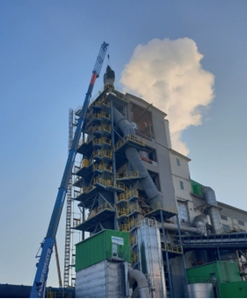
Hình 12. Lắp đặt chi tiết cuối cùng của calciner vào cuối năm 2018.
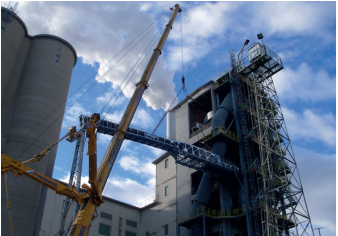
Hình 13. Thi công lắp đặt tại calciner (Cầu băng tải SSW được đấu nối với kết cấu calciner mới).
Trong lần dừng lò năm 2019, buồng đầu vào lò nung và các cyclone C4 đã được tháo dỡ, lắp vào các cyclone tầng đáy và việc định tuyến bột liệu đã được thực hiện để cho phép đấu nối calciner với hệ thống. Lò nung cũng đã được cắt và đường nhánh gió ba (chụp lò) đã được lắp với máy làm nguội. Điều này đã được thực hiện trong lần dừng lò 8 tuần (các Hình 12 - 13).
Kết quả
Việc tái triển khai và vận hành thành công đã được thực hiện trong tháng 4/2019 theo tiến độ của dự án. Các kết quả vận hành đã khẳng định các giá trị công nghệ đã tính toán trước đó và đã cho thấy được mọi điều kể cả những cải tiến thêm nữa. Tóm lại, những khác biệt quan sát được trong quá trình chạy bảo hành như sau:
- Vận hành đạt 100% mức nhiên liệu thay thế cả ở calciner lẫn ở vòi đốt chính.
- Sản lượng clinker sản xuất đạt 1400 tấn/ngày.
- Phát thải NOx < 190 mg/Nm³ duy trì được độ trượt NH3 xấp xỉ 22 mg/Nm³.
- Phát thải CO < 560 mg/Nm³.
Vì là chuyển đổi từ lò nung có thiết bị sấy sơ bộ sang lò nung calcinker nên dẫn đến sự thay đổi đáng kể về quy trình vận hành và các thông số đã được biết đến đối với hệ thống này, điều đáng chú hơn là đội ngũ nhân viên vận hành và các kỹ sư tại Lafarge Retznei đã xoay xở khởi động suôn sẻ tất cả các hệ thống và calciner trong thời gian gia nhiệt hệ thống. Điều đặc biệt cần lưu ý là việc chuyển đổi sang đốt 100% nhiên liệu thay thế tại calciner đã được kiểm soát ngay sau khi bắt đầu sản xuất clinker trong khoảng 1 tuần. Ngoài ra, tổng thể dự án đã hoàn toàn đi đúng hướng và sản lượng cao nhất đã đạt được theo kế hoạch.
Tài liệu tham khảo
1. RAHMAN, A., RASUL, M.G, KHAN, M.M.K, SHARMA, S., ‘Recent development on the uses of alternative fuels in cement manufacturing process’, Fuel, 2015, 145, pp.84 - 99.
2. BODENDIEK, N., NOx-Minderung durch gestufte Verbrennung und deren Wechselwirkung mit dem SNCR-Verfahren bei Vorcalcinieranlagen der Zementindustrie’, VDZ, Schriftreihe der Zementindustrie, 2005, 68.
3. SRF production facility saves one million tons of CO2’, ZKG – Cement Lime Gypsum, 5/2018.
4. WEICHINGER, M., & SCHÖFFMANN, H., ‘Suitability of different chlorine bypass systems for practical application’, Cement International, 01, 2002.
5. KERN, S., ‘A New Calciner Design’, World Cement, 11, 2017, pp. 95 – 101.
Để đạt được các mục tiêu này, các tiến trình thực hiện dưới đây đã được áp dụng:
1. Calciner nội tuyến mới đã không thể đặt được vào bên trong tòa nhà công trình hiện có; do đó, nó đã được đặt ở phía trước tháp sấy sơ bộ hiện có trong một kết cấu thép mới (Hình 3).
Thách thức là, như trong rất nhiều hệ thống calciner được trang bị thêm, phải đạt được tất cả các độ nghiêng cho các góc và các mặt cắt nhỏ đã biết nhằm đảm bảo các điều kiện vận hành phù hợp và giảm thiểu hồi lưu bột liệu và tích tụ liệu ở những khu vực đã biết.
Vì hệ thống sấy sơ bộ là một hệ thống hai nhánh nên đã quyết định rằng đầu trên calciner sẽ được thiết kế như một calciner thông thường, được chia nhánh tại đỉnh ở buồng đốt sau (PCC) A TEC thành hai ống dẫn xuống dưới đối xứng nhau, mỗi ống đi vào một trong hai cyclone tầng đáy.
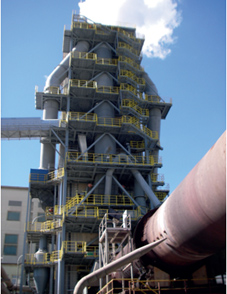
Hình 5. Calciner nội tuyến mới đã hoàn thành tại Retznei.
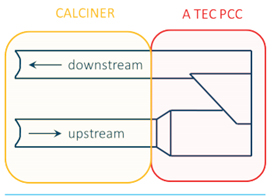
Hình 6. Sơ đồ Buồng Đốt Sau của A TEC (PCC).
Để có thể đấu nối calciner mới với lò nung ở phía đầu vào và với sấy sơ bộ ở phía đầu ra, các điểm đấu nối ở sấy sơ bộ đã được thiết kế lại hoàn toàn. Các cyclone tầng đáy là hai cyclone được thiết kế mới, có đường kính lớn hơn để tăng hiệu suất quá trình lên do dòng khí có thể cao hơn được tạo ra do gia tăng sử dụng SSW sau khi điều chỉnh. Hơn nữa, các đầu vào được xoay 90° và hai nhánh calciner phía dưới đi vào hai cyclone tầng đáy từ bên trái và bên phải tháp sấy sơ bộ thay vì từ phía trước để đảm bảo độ dốc các góc và tránh được các đầu vào cyclone phẳng.
Để đấu nối calciner với lò nung, lò nung đã được cắt ngắn đi khoảng 3m. Điều này cho phép di chuyển buồng đầu vào lò nung về phía trước tòa nhà sấy sơ bộ và tạo được độ dốc nghiêng cho phần đấu nối của calciner với phần vòi phun.
Toàn cảnh calciner sau khi điều chỉnh có thể thấy ở Hình 5.
2. Các đầu vào nhiên liệu của ba loại nhiên liệu (dung môi, than cốc/than và SSW) đã được bố trí tại khu vực đầu vào gió ba thấp hơn để bắt cháy thuận lợi. Đầu vào gió ba thứ hai đã được bố trí cao hơn ở phần phía trên của calciner. Ở khu vực này, vùng khử giảm được hình thành, mà phía sau đầu vào gió ba thứ hai được oxi hóa nhưng vẫn hoạt động phần nào trong vài giây. Để đốt cháy hết một cách an toàn bất kỳ nhiên liệu nào chưa cháy và CO, xuất phát từ vùng khử giảm NOx, thời gian lưu khí vừa đủ trong calciner là cần thiết. Thiết kế calciner được lựa chọn ở đây cho thấy một tính năng mà tránh được việc cần đến các calciner rất lớn, và mang lại kết quả mà có thể đạt được với thời gian lưu thực tế hợp lý. Tính năng này được gọi là Buồng Đốt Sau (PCC).5 Thiết kế của PCC cho thấy những đặc điểm sau: Ở dòng hướng lên của PCC, đường kính được nâng lên để tăng thêm thời gian lưu cho các hạt mà chưa hoàn toàn cháy hết (Hình 6). Đầu vào phần phía dưới calciner được thiết kế lệch tâm để tạo ra sự rối loạn và hiệu quả phối trộn như đã chỉ ra ở mô hình dòng chảy trong Hình 7. Nhìn từ trên xuống PCC ở nhà máy Retznei được thể hiện ở Hình 8. Điều này mang lại hiệu quả là vật chất chưa cháy và các khí (CO...) được phối trộn hiệu quả với khí đốt chưa dùng hết và hoàn thành việc đốt cháy chúng trước khi đi vào các cyclone sấy sơ bộ. Tổng thời gian lưu khí thiết lập trong calciner là 5,9 giây, thấp hơn nhiều so với các hệ thống thông thường để đạt được các thông số hiệu suất yêu cầu về đốt cháy hết và khử giảm NOx.
3. Nhánh phụ Cl hiện có đã được thiết kế ban đầu cho tỷ lệ nhánh phụ là 5% khi đưa vào vận hành cho lò nung có thiết bị sấy sơ bộ. Nhánh phụ này đã được nâng cấp cải tạo nhằm đạt được tỷ lệ nhánh phụ xấp xỉ 10% để có thể xử lý Cl đầu vào tăng lên do tỷ lệ SSW cao hơn. Vì khí đốt riêng cho lò ở đầu vào lò nung gần bằng một nửa lượng khí đốt cho vận hành calciner so với vận hành sấy sơ bộ, có thể tăng lượng khí đốt này lên bằng cách lắp một chụp rẽ nhánh thích hợp và một tầng làm nguội mới. Lọc bụi và quạt bypass hiện có có thể sử dụng như một lượng khí đốt tuyệt đối gần giống như trước khi điều chỉnh.
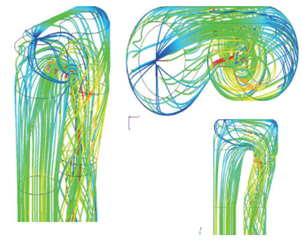
Hình 7. Mô hình dòng chạy được lập theo CFD trong PCC.
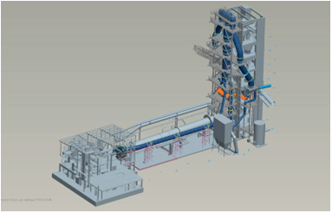
Hình 8. Nhìn từ trên xuốn dưới calciner (PCC) ở Retznei.
4. Hệ thống nhiên liệu cho SSW đã đặt ra thách thức không chỉ đối với việc định lượng nguyên liệu ổn định cho hệ thống, mà còn vận chuyển nó từ cơ sở chuẩn bị của Thermoteam nằm cách đó gần 250 m. A TEC đã lựa chọn băng tải chữ U để thực hiện công việc này. Băng tải này tương tự như băng tải ống, nhưng phần băng tải mà trong đó liệu được vận chuyển là phần được mở ra ở trên cùng (băng tải được uốn cong thành hình chữ U) và được đậy nắp riêng để tránh tràn liệu. Băng tải quay về được đậy kín hoàn toàn để tránh tràn liệu. Băng tải được đậy kín từng phần mang lại những lợi ích vận hành vì nó không nhạy cảm với nguyên liệu quá cỡ mà nếu không sẽ gây thủng băng. Hình 9 chỉ ra một phần băng tải chữ U và Hình 10 cho thấy các két định lượng tới băng tải.
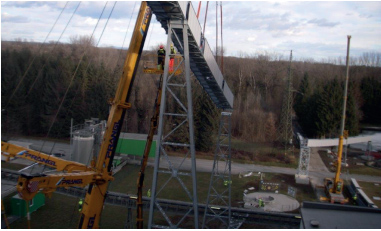
Hình 9. Lắp đặt băng tải cho SSW từ hạng mục công trình Thermoteam (cơ sở chuẩn bị) tới điểm cấp liệu calciner.
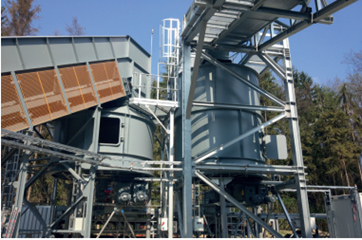
Hình 10. Các két định lượng cho SSW tới băng tải.
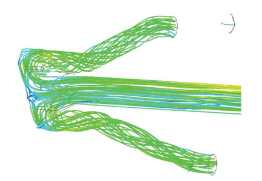
Hình 11. Lập mô hình hình học CFD (các dòng chảy - màu sắc biểu đạt vận tốc).
Đo lường nguyên liệu được thực hiện tại đầu vào băng tải chữ U bởi một két chứa phía trước có thiết bị khuấy trên tế bào tải. Băng tải chữ U có thể được chất tải đồng thời từ thiết bị Thermoteam hoặc từ trạm dỡ tải lên xe tải mới để đạt được sự linh hoạt cao nhất.
5. Một hệ thống mới hoàn toàn, tùy biến đã được lắp đặt để vận chuyển và định lượng các nhiên liệu thay thế dạng lỏng (LAF, dung môi). Vì một trong những điều kiện biên đó là có thể xuất hiện các hạt có kích thước lên đến 5mm, một hệ thống đặc biệt đã được thiết kế trong đó tốc độ dòng thể tích được kiểm soát hoàn toàn nhờ một máy bơm kiểu pittong điều tốc, tránh tạo áp cho bất kỳ thiết bị nào trong hệ thống dẫn tới vòi phun. Riêng đối với vòi phun, cái gọi là ‘vòi phun buồng hở’ đã được sử dụng để phun chất lỏng bằng khí nén; kết quả là có thể nhìn thấy lỗ mở vòi phun lớn.
6. Hệ thống SNCR là một tiêu điểm của quá trình riêng biệt. Như đã trình bày ở trên, hệ thống sẽ phải được thiết kế sao cho đạt được hiệu suất tối đa nhưng cũng phải lắp được vào trong calciner để cho phép:
- Giảm thiểu ảnh hưởng tới quá trình khử giảm NOx sơ cấp thông qua việc đốt cháy từng bậc và chỉ xử lý những lượng NOx sót lại sau khi đốt từng bậc.
- Xử lý được cả lượng thấp (SSW/LAF hoạt động) lẫn lượng cao (than cốc) NOx cơ sở.
- Đạt được độ trượt ammonia thấp.
Khái niệm được lựa chọn là để phun vào phần phía dưới của calciner theo hai cấp độ. Cấp độ thứ nhất là ngay phía trước đầu vào mỗi cyclone tầng 4, cấp độ thứ hai là đầu vào cấp độ thứ nhất nói trên. Trong quá trình vận hành đốt bằng than cốc cho calciner, cấp độ thứ hai của vòi phun có thể được kích hoạt.
Thiết kế hoàn chỉnh calciner, bao gồm cả định vị vòi phun, đã được kiểm tra thông qua phân tích CFD để xác thực các kết quả tính toán (Hình 11)
A TEC Production and Services GmbH là nhà thầu thi công chính cho dự án trên cơ sở EPC cơ khí. Công ty đã chịu trách nhiệm về thiết kế hoàn chỉnh, tháo dỡ, gia công chế tạo và lắp đặt kết cấu thép và thiết bị bao gồm cả các công việc và các dịch vụ cần thiết tại hiện trường thi công.
Các công tác thi công lắp dựng cơ khí tại hiện trường nhà máy Retznei đã bắt đầu thực hiện vào cuối mùa hè năm 2018 với việc lắp dựng kết cấu thép cho caclciner mới tiếp theo là lắp đặt calciner. Cả hai công việc đều đã được hoàn thành trong tháng 12/2018.
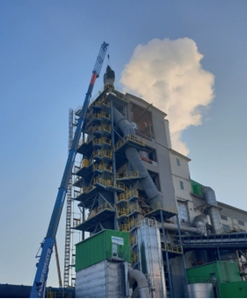
Hình 12. Lắp đặt chi tiết cuối cùng của calciner vào cuối năm 2018.
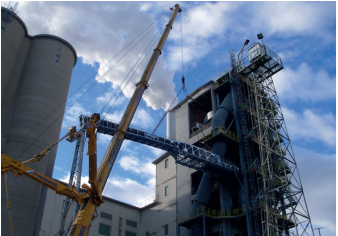
Hình 13. Thi công lắp đặt tại calciner (Cầu băng tải SSW được đấu nối với kết cấu calciner mới).
Trong lần dừng lò năm 2019, buồng đầu vào lò nung và các cyclone C4 đã được tháo dỡ, lắp vào các cyclone tầng đáy và việc định tuyến bột liệu đã được thực hiện để cho phép đấu nối calciner với hệ thống. Lò nung cũng đã được cắt và đường nhánh gió ba (chụp lò) đã được lắp với máy làm nguội. Điều này đã được thực hiện trong lần dừng lò 8 tuần (các Hình 12 - 13).
Kết quả
Việc tái triển khai và vận hành thành công đã được thực hiện trong tháng 4/2019 theo tiến độ của dự án. Các kết quả vận hành đã khẳng định các giá trị công nghệ đã tính toán trước đó và đã cho thấy được mọi điều kể cả những cải tiến thêm nữa. Tóm lại, những khác biệt quan sát được trong quá trình chạy bảo hành như sau:
- Vận hành đạt 100% mức nhiên liệu thay thế cả ở calciner lẫn ở vòi đốt chính.
- Sản lượng clinker sản xuất đạt 1400 tấn/ngày.
- Phát thải NOx < 190 mg/Nm³ duy trì được độ trượt NH3 xấp xỉ 22 mg/Nm³.
- Phát thải CO < 560 mg/Nm³.
Vì là chuyển đổi từ lò nung có thiết bị sấy sơ bộ sang lò nung calcinker nên dẫn đến sự thay đổi đáng kể về quy trình vận hành và các thông số đã được biết đến đối với hệ thống này, điều đáng chú hơn là đội ngũ nhân viên vận hành và các kỹ sư tại Lafarge Retznei đã xoay xở khởi động suôn sẻ tất cả các hệ thống và calciner trong thời gian gia nhiệt hệ thống. Điều đặc biệt cần lưu ý là việc chuyển đổi sang đốt 100% nhiên liệu thay thế tại calciner đã được kiểm soát ngay sau khi bắt đầu sản xuất clinker trong khoảng 1 tuần. Ngoài ra, tổng thể dự án đã hoàn toàn đi đúng hướng và sản lượng cao nhất đã đạt được theo kế hoạch.
Tài liệu tham khảo
1. RAHMAN, A., RASUL, M.G, KHAN, M.M.K, SHARMA, S., ‘Recent development on the uses of alternative fuels in cement manufacturing process’, Fuel, 2015, 145, pp.84 - 99.
2. BODENDIEK, N., NOx-Minderung durch gestufte Verbrennung und deren Wechselwirkung mit dem SNCR-Verfahren bei Vorcalcinieranlagen der Zementindustrie’, VDZ, Schriftreihe der Zementindustrie, 2005, 68.
3. SRF production facility saves one million tons of CO2’, ZKG – Cement Lime Gypsum, 5/2018.
4. WEICHINGER, M., & SCHÖFFMANN, H., ‘Suitability of different chlorine bypass systems for practical application’, Cement International, 01, 2002.
5. KERN, S., ‘A New Calciner Design’, World Cement, 11, 2017, pp. 95 – 101.
Tiến sỹ Stefan Kern, A TEC Production and Services GmbH
Nguyễn Thị Kim Lan dịch từ Tạp chí World Cement số tháng 6/2022
ximang.vn
Nguyễn Thị Kim Lan dịch từ Tạp chí World Cement số tháng 6/2022
ximang.vn