Giảm thiểu phát thải, gia tăng sử dụng tối đa nhiên liệu thay thế (P1)
Trong bài viết này, Tiến sỹ Stefan Kern, A TEC Production and Services GmbH, trình bày chi tiết dự án chuyển đổi lò nung tại Lafarge Retznei và cách thức mà thiết kế calciner được tối ưu hóa cho phép sử dụng 100% nhiên liệu thay thế ra sao.
>> Giảm thiểu phát thải, gia tăng sử dụng tối đa nhiên liệu thay thế (P2)
Để giảm thiểu tác động môi trường gây ra bởi quá trình sản xuất xi măng, mọi nỗ lực lúc này là hướng tới việc giảm thiểu phát thải cùng với sự linh hoạt trong sử dụng nhiên liệu, và tiết kiệm nhiên liệu.
Sử dụng nhiên liệu thay thế đóng một vai trò quan trọng trong việc giảm thiểu phát thải CO2 gây ra bởi các nhiên liệu hóa thạch cũng như việc giảm bớt sự phụ thuộc vào nhiên liệu hóa thạch nói chung.
Tuy nhiên, việc sử dụng các nhiên liệu rắn thay thế đặt ra một số thách thức cho quá trình chế tạo clinker, như thông qua tác động lên chính quá trình đốt, và cũng thông qua các thành phần vi lượng được đưa vào, chẳng hạn như clo. Do tính chất của các nhiên liệu rắn thay thế, sự tác động tới phát thải CO nói chung có thể quan sát được qua việc tăng TSR (mức thay thế nhiệt), mà đối với vòi đốt chính thường dẫn đến sự hạn chế trong việc sử dụng chúng hoặc, đối với calciner, trong các hệ thống quy mô lớn cho phép đốt cháy hoàn toàn nhiên liệu.1
Ngoài các quy định của quốc gia, rất nhiều nhà sản xuất xi măng cũng đã cam kết giảm thiểu phát thải NOx và CO (cùng với các phát thải khác). Trong trường hợp nhà máy Lafarge tại Retznei, mục đích là để đạt được mức NOx ở ống khói dưới 200 mg/Nm³ và mức CO nhỏ hơn 1000 mg/Nm³.
Các calciner nội tuyến (ILC) là lựa chọn được ưa thích khi đề cập đến việc sử dụng các nhiên liệu rắn thay thế. Không giống như các hệ thống calciner dòng riêng (SLC), trong đó các hạt nhiên liệu nặng rơi vào trong khuỷu nối ống gió ba, các hệ thống ILC có thể xử lý các hạt nhiên liệu lớn hơn và những mảnh nặng (nếu bị hạn chế ở mức độ là một thành phần thứ yếu) có thể rơi xuống qua vòi phun và cháy trực tiếp trong lò mà không ảnh hưởng tới quá trình vận hành.
Được biết phát thải Nox là do quá trình nung luyện clinker gây ra. Do nhiệt độ zôn nung cần thiết trong lò (tối thiểu 1450°C, phụ thuộc vào thành phần nguyên liệu), cửa sổ hình thành Nox nhiệt - trong đó nitơ trong khí đốt bị oxi hóa - được đưa vào và một lượng đáng kể phát thải NOx được hình thành trong lò. Các giải pháp xử lý NOx lò nung là thông qua các phép đo sơ cấp trong calciner nội tuyến, hệ thống khử giảm như SNCR, hệ thống SCR, hoặc sự kết hợp giữa các phép đo sơ cấp và thứ cấp.
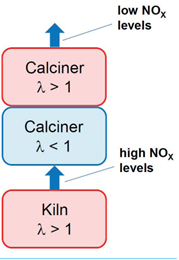
Hình 1. Nguyên lý đốt từng cấp trong hệ thống lò nung có calciner nội tuyến.
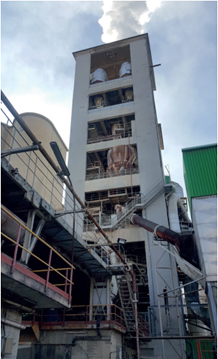
Hình 2. Sấy sơ bộ trước khi điều chỉnh.
Hình 3. Mô hình 3D của hệ thống mới có calciner nội tuyến mới (Các chi tiết mới/đã điều chỉnh được thể hiện bằng màu xanh da trời)
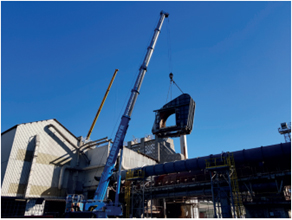
Hình 4. Lắp đặt chụp lò tại máy làm nguội clinker cho đường nhánh gió ba.
Để giảm thiểu tác động môi trường gây ra bởi quá trình sản xuất xi măng, mọi nỗ lực lúc này là hướng tới việc giảm thiểu phát thải cùng với sự linh hoạt trong sử dụng nhiên liệu, và tiết kiệm nhiên liệu.
Sử dụng nhiên liệu thay thế đóng một vai trò quan trọng trong việc giảm thiểu phát thải CO2 gây ra bởi các nhiên liệu hóa thạch cũng như việc giảm bớt sự phụ thuộc vào nhiên liệu hóa thạch nói chung.
Tuy nhiên, việc sử dụng các nhiên liệu rắn thay thế đặt ra một số thách thức cho quá trình chế tạo clinker, như thông qua tác động lên chính quá trình đốt, và cũng thông qua các thành phần vi lượng được đưa vào, chẳng hạn như clo. Do tính chất của các nhiên liệu rắn thay thế, sự tác động tới phát thải CO nói chung có thể quan sát được qua việc tăng TSR (mức thay thế nhiệt), mà đối với vòi đốt chính thường dẫn đến sự hạn chế trong việc sử dụng chúng hoặc, đối với calciner, trong các hệ thống quy mô lớn cho phép đốt cháy hoàn toàn nhiên liệu.1
Ngoài các quy định của quốc gia, rất nhiều nhà sản xuất xi măng cũng đã cam kết giảm thiểu phát thải NOx và CO (cùng với các phát thải khác). Trong trường hợp nhà máy Lafarge tại Retznei, mục đích là để đạt được mức NOx ở ống khói dưới 200 mg/Nm³ và mức CO nhỏ hơn 1000 mg/Nm³.
Các calciner nội tuyến (ILC) là lựa chọn được ưa thích khi đề cập đến việc sử dụng các nhiên liệu rắn thay thế. Không giống như các hệ thống calciner dòng riêng (SLC), trong đó các hạt nhiên liệu nặng rơi vào trong khuỷu nối ống gió ba, các hệ thống ILC có thể xử lý các hạt nhiên liệu lớn hơn và những mảnh nặng (nếu bị hạn chế ở mức độ là một thành phần thứ yếu) có thể rơi xuống qua vòi phun và cháy trực tiếp trong lò mà không ảnh hưởng tới quá trình vận hành.
Được biết phát thải Nox là do quá trình nung luyện clinker gây ra. Do nhiệt độ zôn nung cần thiết trong lò (tối thiểu 1450°C, phụ thuộc vào thành phần nguyên liệu), cửa sổ hình thành Nox nhiệt - trong đó nitơ trong khí đốt bị oxi hóa - được đưa vào và một lượng đáng kể phát thải NOx được hình thành trong lò. Các giải pháp xử lý NOx lò nung là thông qua các phép đo sơ cấp trong calciner nội tuyến, hệ thống khử giảm như SNCR, hệ thống SCR, hoặc sự kết hợp giữa các phép đo sơ cấp và thứ cấp.
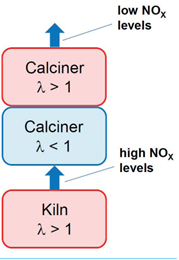
Hình 1. Nguyên lý đốt từng cấp trong hệ thống lò nung có calciner nội tuyến.
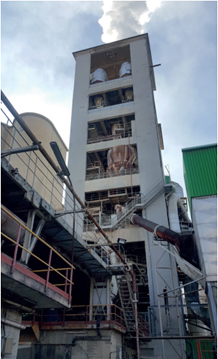
Hình 2. Sấy sơ bộ trước khi điều chỉnh.
Chỉ có ILC có khả năng khử giảm được phát thải NOx lò nung với các phép đo sơ cấp, không giống như trong SLC, toàn bộ lượng khí lò nung (ngoại trừ khí được làm sạch bằng nhánh phụ Cl) đi qua calciner và có thể đi qua quá trình đốt từng bậc trong calciner. Điều này được thực hiện với một phần khí đốt (gió ba), tạo ra một vùng khử giảm ở đầu vào calciner nơi phun nhiên liệu cấp cho calciner vào (Hình 1). Ở vùng này, các phân tử NOx có thể bị khử bởi CO và các gốc nguyên liệu, được thể hiện qua các phản ứng sau:
► CO + NO = CO2 + 0,5 N2
► CxHy + zNO = xCO2 + y/2 H2O + z/2 N2
Để tối đa hóa các phản ứng này, hàm lượng CO/các gốc hydrocarbon cần phải phù hợp, nhiệt độ phải cao vừa đủ và đặc tính dòng chảy trong calciner phải tạo điều kiện cho phối trộn tốt các thành phần. Để đạt được các giá trị thậm chí thấp hơn, cũng có thể trang cấp hệ thống SNCR cho các calciner này.2
Chương trình khử giảm NOx này tạo ra sự khác biệt liên quan tới phát thải CO vì chúng cần thiết cho khử giảm NOx. Hơn nữa, CO được biết đến là ức chế phản ứng trong hệ thống phun ammonia/urea của SNCR. Do đó, việc thiết kế calciner cho mục tiêu phát thải như vậy, đồng thời đáp ứng khả năng sử dụng 100% nhiên liệu thay thế, đòi hỏi phải kết hợp nhiều phương diện thiết kế.
Trong trường hợp áp dụng đối với dây chuyền lò nung tại Lafarge Retznei, Áo, hệ thống này đã được chuyển đổi hoàn toàn từ lò nung có thiết bị sấy sơ bộ sang lò nung ILC để tạo ra hệ thống lò nung tiêu chuẩn cho phát thải và sử dụng nhiên liệu thay thế. Hệ thống calciner đã được A TEC Production & Services GmbH phát triển và lắp đặt vào năm 2018/2019.
Sản xuất clinker tại Lafarge Retznei và tình hình trước khi điều chỉnh
Trước khi điều chỉnh, Lafarge đã vận hành dây chuyền lò nung ở Retzne, Áo, là một lò nung xi măng xám với công suất sản xuất 1400 tấn/ngày. Sấy sơ bộ là một hệ thống bốn tầng hai nhánh, không có calciner. Cho dù không có calciner và ống gió ba, nhà máy đã đặt ra tiêu chuẩn đối với các lò có thiết bị sấy sơ bộ để sử dụng nhiên liệu thay thế và nhà máy được ghi nhận rộng rãi trên thế giới về điều này. Tại vòi đốt chính, hỗn hợp than cốc, SSW (phế thải nhựa rắn nghiền vụn), dầu thải, dung môi, thức ăn động vật và xơ lốp xe được đốt tại đây. Với việc bổ sung thêm lốp xe toàn chiếc tại đầu vào lò nung, đã đạt được một lượng TSR đáng kể tới 96% trước khi tiến hành điều chỉnh. SSW được Thermoteam, một liên danh giữa Lafarge và công ty Saubermacher, sản xuất ra trực tiếp bên cạnh nhà máy. Một hệ băng tải ống đưa SSW trực tiếp từ nhà máy chuẩn bị tới vòi đốt chính. Trước khi tiến hành điều chỉnh, trung bình hàng năm phát thải NOx là ~400 mg/Nm³ và giá trị CO là khoảng 1800 mg/Nm³. Sấy sơ bộ trước khi điều chỉnh có thể thấy ở Hình 2.
Triển khai dự án và mô tả dự án
Vì những lý do được trình bày ở trên, nhà máy đã bị hạn chế trong việc xử lý phát thải NOx và CO và hướng tới mục tiêu đạt 200 mg/Nm³ NOx và <1000 mg/Nm³ phát thải CO tại ống khói.
Đồng thời, giải pháp tiếp cận cũng nhằm mục đích tăng mức sử dụng TSR nhiều hơn và vận hành với mức thay thế nhiệt thường xuyên 100%. Điều này có nghĩa rằng giải pháp tiếp cận này lên kế hoạch để chuyển đổi đáng kể hỗn hợp nhiên liệu sang SSW từ khoảng 39% lên 77% tổng hỗn hợp nhiên liệu. Các nhiên liệu khác cũng đã có kế hoạch giảm bớt, như lốp xe, than cốc và dầu/các dung môi. Kết quả sau khi điều chỉnh sẽ là TSR đạt xấp xỉ 100%/năm.
Nhà máy đã được trang bị một hệ thống Nhánh phụ Cl (Cl-Bypass) của A TEC, được lắp đặt vào năm 2001 và vẫn hoạt động từ đó đến nay.4 Khi nhánh phụ lọc sạch khí từ đầu vào lò, nơi có hàm lượng NOx rất cao, phần khí nhánh phụ này không thể xử lý được trong calciner hoặc bằng hệ thống SNCR. Khí nhánh phụ, được trộn lẫn với khí làm nguội, sau bộ lọc nhánh phụ được trộn lẫn với khí thải sấy sơ bộ. Để đạt được giá trị phát thải NOx dưới 200 mg/Nm³ tại ống khói, khí thải từ sấy sơ bộ (calciner) phải đạt các giá trị thậm chí còn thấp hơn để bù khuyết cho ảnh hưởng này và đạt được giá trị mục tiêu.
Trong trường hợp nhà máy Retznei, hệ thống lò nung và calciner phải đạt hàm lượng NOx < 180 mg/Nm³. Đây là một thách thức nữa đối với hệ thống calciner và SNCR để đạt được các giá trị cơ bản thậm chí thấp hơn và đạt được giá trị mục tiêu 200mg/Nm3 phát thải NOx tại ống khói trong suốt quá trình vận hành.
Tóm tắt tình hình trong giai đoạn triển khai, các công đoạn chính của dự án như sau:
► Lắp đặt calciner nội tuyến:
• Khả năng đốt cháy SSW, dung môi và than/than cốc, mỗi loại lên đến 100%.
• Kích thước hạt SSW lên đến 80mm (2D).
► Hoàn thành các hệ thống vận chuyển và định lượng nhiên liệu mới cho SSW, dung môi và than/than cốc.
► Lắp đặt đường nhánh gió ba tại máy làm nguội bao gồm cả điều chỉnh chụp lò và hệ thống đường ống gió ba.
► Buồng đầu vào lò nung mới và điều chỉnh lò nung.
► Các cyclone tầng đáy mới và hệ thống đường ống bột liệu được tối ưu hóa.
► Hệ thống phun SNCR mới và chuyển đổi hệ thống SNCR từ urea sang NH3.
Nâng cấp cải tạo bộ truyền động lò để nâng tốc độ lò từ mức cao nhất 2,5 vòng/phút lên 3,8 vòng/phút để điều chỉnh thời gian lưu liệu do quá trình tiền nung.
► CO + NO = CO2 + 0,5 N2
► CxHy + zNO = xCO2 + y/2 H2O + z/2 N2
Để tối đa hóa các phản ứng này, hàm lượng CO/các gốc hydrocarbon cần phải phù hợp, nhiệt độ phải cao vừa đủ và đặc tính dòng chảy trong calciner phải tạo điều kiện cho phối trộn tốt các thành phần. Để đạt được các giá trị thậm chí thấp hơn, cũng có thể trang cấp hệ thống SNCR cho các calciner này.2
Chương trình khử giảm NOx này tạo ra sự khác biệt liên quan tới phát thải CO vì chúng cần thiết cho khử giảm NOx. Hơn nữa, CO được biết đến là ức chế phản ứng trong hệ thống phun ammonia/urea của SNCR. Do đó, việc thiết kế calciner cho mục tiêu phát thải như vậy, đồng thời đáp ứng khả năng sử dụng 100% nhiên liệu thay thế, đòi hỏi phải kết hợp nhiều phương diện thiết kế.
Trong trường hợp áp dụng đối với dây chuyền lò nung tại Lafarge Retznei, Áo, hệ thống này đã được chuyển đổi hoàn toàn từ lò nung có thiết bị sấy sơ bộ sang lò nung ILC để tạo ra hệ thống lò nung tiêu chuẩn cho phát thải và sử dụng nhiên liệu thay thế. Hệ thống calciner đã được A TEC Production & Services GmbH phát triển và lắp đặt vào năm 2018/2019.
Sản xuất clinker tại Lafarge Retznei và tình hình trước khi điều chỉnh
Trước khi điều chỉnh, Lafarge đã vận hành dây chuyền lò nung ở Retzne, Áo, là một lò nung xi măng xám với công suất sản xuất 1400 tấn/ngày. Sấy sơ bộ là một hệ thống bốn tầng hai nhánh, không có calciner. Cho dù không có calciner và ống gió ba, nhà máy đã đặt ra tiêu chuẩn đối với các lò có thiết bị sấy sơ bộ để sử dụng nhiên liệu thay thế và nhà máy được ghi nhận rộng rãi trên thế giới về điều này. Tại vòi đốt chính, hỗn hợp than cốc, SSW (phế thải nhựa rắn nghiền vụn), dầu thải, dung môi, thức ăn động vật và xơ lốp xe được đốt tại đây. Với việc bổ sung thêm lốp xe toàn chiếc tại đầu vào lò nung, đã đạt được một lượng TSR đáng kể tới 96% trước khi tiến hành điều chỉnh. SSW được Thermoteam, một liên danh giữa Lafarge và công ty Saubermacher, sản xuất ra trực tiếp bên cạnh nhà máy. Một hệ băng tải ống đưa SSW trực tiếp từ nhà máy chuẩn bị tới vòi đốt chính. Trước khi tiến hành điều chỉnh, trung bình hàng năm phát thải NOx là ~400 mg/Nm³ và giá trị CO là khoảng 1800 mg/Nm³. Sấy sơ bộ trước khi điều chỉnh có thể thấy ở Hình 2.
Triển khai dự án và mô tả dự án
Vì những lý do được trình bày ở trên, nhà máy đã bị hạn chế trong việc xử lý phát thải NOx và CO và hướng tới mục tiêu đạt 200 mg/Nm³ NOx và <1000 mg/Nm³ phát thải CO tại ống khói.
Đồng thời, giải pháp tiếp cận cũng nhằm mục đích tăng mức sử dụng TSR nhiều hơn và vận hành với mức thay thế nhiệt thường xuyên 100%. Điều này có nghĩa rằng giải pháp tiếp cận này lên kế hoạch để chuyển đổi đáng kể hỗn hợp nhiên liệu sang SSW từ khoảng 39% lên 77% tổng hỗn hợp nhiên liệu. Các nhiên liệu khác cũng đã có kế hoạch giảm bớt, như lốp xe, than cốc và dầu/các dung môi. Kết quả sau khi điều chỉnh sẽ là TSR đạt xấp xỉ 100%/năm.
Nhà máy đã được trang bị một hệ thống Nhánh phụ Cl (Cl-Bypass) của A TEC, được lắp đặt vào năm 2001 và vẫn hoạt động từ đó đến nay.4 Khi nhánh phụ lọc sạch khí từ đầu vào lò, nơi có hàm lượng NOx rất cao, phần khí nhánh phụ này không thể xử lý được trong calciner hoặc bằng hệ thống SNCR. Khí nhánh phụ, được trộn lẫn với khí làm nguội, sau bộ lọc nhánh phụ được trộn lẫn với khí thải sấy sơ bộ. Để đạt được giá trị phát thải NOx dưới 200 mg/Nm³ tại ống khói, khí thải từ sấy sơ bộ (calciner) phải đạt các giá trị thậm chí còn thấp hơn để bù khuyết cho ảnh hưởng này và đạt được giá trị mục tiêu.
Trong trường hợp nhà máy Retznei, hệ thống lò nung và calciner phải đạt hàm lượng NOx < 180 mg/Nm³. Đây là một thách thức nữa đối với hệ thống calciner và SNCR để đạt được các giá trị cơ bản thậm chí thấp hơn và đạt được giá trị mục tiêu 200mg/Nm3 phát thải NOx tại ống khói trong suốt quá trình vận hành.
Tóm tắt tình hình trong giai đoạn triển khai, các công đoạn chính của dự án như sau:
► Lắp đặt calciner nội tuyến:
• Khả năng đốt cháy SSW, dung môi và than/than cốc, mỗi loại lên đến 100%.
• Kích thước hạt SSW lên đến 80mm (2D).
► Hoàn thành các hệ thống vận chuyển và định lượng nhiên liệu mới cho SSW, dung môi và than/than cốc.
► Lắp đặt đường nhánh gió ba tại máy làm nguội bao gồm cả điều chỉnh chụp lò và hệ thống đường ống gió ba.
► Buồng đầu vào lò nung mới và điều chỉnh lò nung.
► Các cyclone tầng đáy mới và hệ thống đường ống bột liệu được tối ưu hóa.
► Hệ thống phun SNCR mới và chuyển đổi hệ thống SNCR từ urea sang NH3.
Nâng cấp cải tạo bộ truyền động lò để nâng tốc độ lò từ mức cao nhất 2,5 vòng/phút lên 3,8 vòng/phút để điều chỉnh thời gian lưu liệu do quá trình tiền nung.
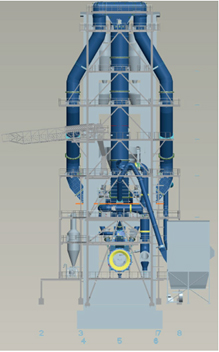
Hình 3. Mô hình 3D của hệ thống mới có calciner nội tuyến mới (Các chi tiết mới/đã điều chỉnh được thể hiện bằng màu xanh da trời)
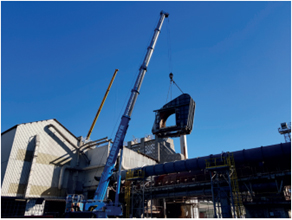
Hình 4. Lắp đặt chụp lò tại máy làm nguội clinker cho đường nhánh gió ba.
Tiến sỹ Stefan Kern, A TEC Production and Services GmbH
Nguyễn Thị Kim Lan dịch từ Tạp chí World Cement số tháng 6/2022
ximang.vn
Nguyễn Thị Kim Lan dịch từ Tạp chí World Cement số tháng 6/2022
ximang.vn