>> Sản xuất pozzolan nhân tạo làm nguyên liệu thay thế cho clinker (P2)
Trong những năm qua, các công ty đã tìm kiếm các mô hình kinh doanh vừa có thể kết hợp cả chiến lược phát triển và bền vững trong một thế giới mang tính toàn cầu và cạnh tranh hơn, nhu cầu thị trường buộc các công ty phải giảm giá bán và cắt giảm chi phí sản xuất để có thể tồn tại.
Pozzolan
Pozzolan có thể được chia làm hai loại: Pozzolan tự nhiên được tìm thấy xung quanh các núi lửa (còn gọi là Pozzolan) và Pozzolan nhân tạo là một loại vật liệu được tạo ra qua quá trình sử dụng lò nung (còn có tên gọi là Pozzolan nung tự nhiên).
Nhiều nhà sản xuất xi măng đã biết đến các vật liệu tương tự Pozzolan như metakaolin, tro bay và xỉ lò cao, tuy nhiên, một số nhà máy đang đầu tư vào việc nung và hoạt hóa các loại đất sét như là một biện pháp để thúc đẩy việc sử dụng pozzolan trong sản xuất xi măng.
Ở mỗi khu vực, thành phần hóa học của đất sét Pozzolan có thể khác nhau, nhưng nói chung hàm lượng silic oxit (SiO2) trong khoảng từ 55% đến 70% và nhôm (Al2O3) từ 15 đến 30%. Điểm quan trọng trong vật liệu này là phải đảm bảo hàm lượng silic ôxit tối đa và phản ứng mạnh nhất với hydroxit canxi. Kết quả của phản ứng là hợp chất calcium silicat có cường độ biến đổi từ một tỷ lệ nhỏ đến gần bằng tỷ lệ của xi măng Porland thông thường.
Ưu điểm của việc sử dụng Pozzolan
Có 4 ưu điểm lớn khi sử dụng Pozzolan, cụ thể như sau:
Tăng năng suất:
Trong sản xuất xi măng, một trong những ưu điểm của việc sử dụng Pozzolan là tăng năng suất so với việc sử dụng lượng clinker tương ứng, giả thiết là một số loại xi măng có thể chứa tới 40% nguyên liệu Pozzolan (theo tiêu chuẩn ASTM C 595). Ở một số nước, con số này có thể đạt tới 50%.
Yêu cầu về đầu tư thấp hơn:
So với dây chuyền sản xuất clinker, dây chuyền sản xuất Pozzolan chiếm chi phí thấp hơn 60%, cần ít thiết bị và ít nhân lực hơn (vận hành và bảo trì) để hoạt động.
Giảm lượng tiêu thụ điện năng và tiêu hao nhiệt:
Không cần máy nghiền liệu (đất sét Pozzolan chỉ cần giảm đến kích thước cục của nó để có thể cấp trực tiếp vào lò) và không đòi hỏi quá trình clinker hóa, nguyên liệu chỉ cần được sấy khô, gia nhiệt tới nhiệt độ 900 độ C (trong khoảng 700 đến 900 độ C, phụthuộc vào loại đất sét) và được hoạt hóa (để tăng độ xốp lên, tăng diện tích bề mặt và phản ứng). Tiêu hao nhiên liệu của một dây chuyền hoạt hóa đất sét Pozzolan thấp hơn nhiều so với dây chuyền clinker.
Lượng phát thải CO2 ít hơn:
Sản xuất 1 kg clinker thường phát thải ra khoảng 0,85kg CO2 (trong đó 0,54kg phát thải từ quá trình phân hủy đá vôi và 0,31kg từ khí thải). Việc hoạt hóa đất sét Pozzolanic không xảy ra ở quá trình phân hủy nhiệt của cacbonat mà đã tồn tại với một tỷ trọng rất lớn.
Ngoài ra, do quá trình sản xuất xi măng chứa Pozzolan yêu cầu ít năng lượng hơn (cả nhiệt và điện), nên lượng CO2 tạo ra cũng thấp hơn đáng kể.
Dây chuyền Pozzolan
Các khách hàng đã đề xuất công ty Dynamis phát triển dây chuyền nung Pozzolan để đốt 100% than cốc đã được nghiền mịn. Nhiên liệu này có sẵn tại các nhà máy của khách hàng, và chỉ được sử dụng dầu nhiên liệu nhẹ để gia nhiệt hệ thống.
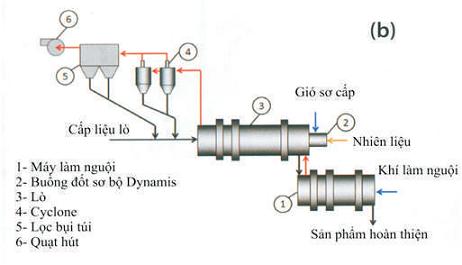
Hình 1: Các giải pháp của Dynamis phù hợp với Dự án này
Những thách thức
Khi đốt cháy các chất rắn đã được nghiền mịn, phải tuân thủ một số điều kiện để đảm bảo quá trình cháy ổn định, thường gọi là ba "T" của quá trình đốt cháy:
- Nhiệt độ (Temperature)
- Thời gian (Time)
- Độ hòa trộn (Turbulence)
Đối với các lò nung clinker, các điều kiện phải phù hợp để đốt tất cả các loại nhiên liệu (bao gồm cả chất rắn đã được nghiền mịn). Với dây chuyền Pozzolan do Dynamis thiết kế, đất sét được sử dụng làm nguyên liệu thô cần thiết để các sản phẩm cuối cùng đạt được chỉ tiêu 1,5% LOI (mất khi nung). Nếu vật liệu được nung hoàn toàn, một phần của nó có thể bị thiêu kết và thuộc tính của xi măng sẽ mất đi. Do đó nhiệt độ quy trình thấp đi đáng kể (lên đến 900 độ C), vì vậy thậm chí với trường hợp có đủ độ hòa trộn, vẫn có những tình huống không đáp ứng được các điều kiện cơ bản để đốt nhiên liệu rắn, gây ra điều kiện vận hành không ổn định (ví dụ ngọn lửa tắt hoặc nhiệt độ quá cao để duy trì lò hoạt động).
Một trong các điều kiện khác rất khó để ổn định là lượng bụi trong lò nung. Đối với dây chuyền sản xuất clinker, ngay cả với các lò có bụi, các yếu tố về độ hòa trộn và nhiệt độ giúp duy trì quá trình cháy ổn định.
Các công nghệ hiện nay được sử dụng để sản xuất đất sét hoạt hóa như Pozzolan có nguồn gốc từ các lò nung clinker và hơn nữa, ngày nay hầu hết các hệ thống hoạt động đều dựa vào các lò nung được trang bị các máy làm nguội kiểu hành tinh.
Đối với dây chuyền Pozzolan, khi nhiệt độ giảm có những lò đã phải dừng tới bốn lần một tuần, do ngọn lửa tắt, và mỗi lần khởi động lại lò - ngoài những hao hụt trong sản xuất - đều yêu cầu thêm nhiên liệu để sấy hệ thống trước khi cấp liệu, vì vậy làm tăng thêm chi phí vận hành. Thành phần nguyên liệu thô được minh họa ở Bảng 1. Đất sét khi tiếp nhận có hàm lượng ẩm trung bình 20% (dạng ướt), cùng với thực tế là hệ số LOI (mất khi nung) của nguyên liệu chủ yếu do nước kết dính hóa học, lò sẽ hoạt động vừa như một thiết bị sấy vừa như một buồng phân hủy (calciner). Với kinh nghiệm sử dụng cả hai hệ thống trên, Dynamis đã bổ sung thêm các giờ nâng liệu được thiết kế đặc biệt, nhờ đó việc trao đổi nhiệt và chất sẽ tăng lên ở đầu dẫn khí của lò, việc sử dụng lò ngắn hơn có thể sẽ rất hiệu quả. Dynamis tận dụng lợi thế độ ẩm của nguyên liệu trong giai đoạn sấy khô để giữ nhiệt độ trên vỏ lò (như là thiết bị sấy), có nghĩa là yêu cầu số lượng gạch chịu lửa sẽ ít hơn.
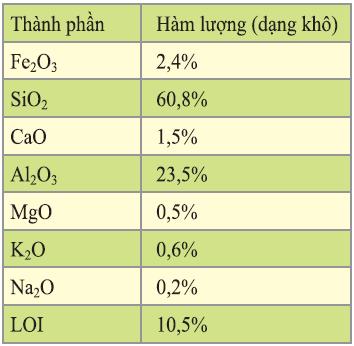
Bảng 1: Thành phần nguyên liệu thô
Máy là nguội kiểu quay được lựa chọn cho ứng dụng này, bở vì gió thứ cấp (làm nguội) đủ để làm nguội sản phẩm và không cần bổ sung thêm khí. Máy làm nguội kiểu ghi thì hiệu quả hơn, nhưng vì nhiệt độ đầu ra của nguyên liệu thấp (xấp xỉ 120 độ C), và phải tính thêm chi phí cũng như mức độ phức tạp của máy làm nguội kiểu ghi, lựa chọn này không đạt hiệu quả về kinh tế.
Máy làm nguội cũng sử dụng một phần nhỏ vật liệu chịu lửa (để tiếp nhận vật liệu nóng từ lò nung) và các gờ nâng liệu để tăng cường trao đổi nhiệt với gió làm nguội (mà sẽ được gia nhiệt và sử dụng như gió thứ cấp của lò).
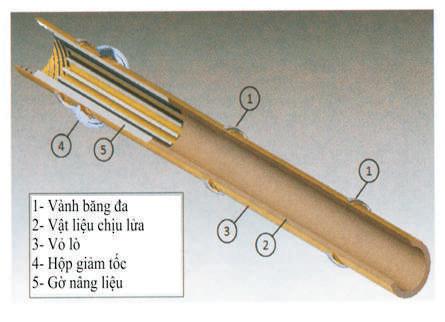
Hình 2: Chi tiết bên trong lò Dynamis
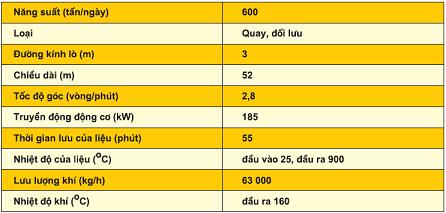
Bảng 2: Các thông số của lò