Đánh giá cân bằng nhiệt hệ thống lò nung clinker (P.1)
Trong công nghiệp, sản xuất xi măng là một trong những hộ tiêu thụ năng lượng lớn, cả về nhiệt năng lẫn điện năng. Chi phí cho năng lượng luôn chiếm một tỉ trọng đáng kể trong cơ cấu giá thành sản phẩm. Vì lẽ đó, khi tìm kiếm các giải pháp nhằm làm giảm chi phí đầu vào, các nhà sản xuất xi măng luôn đặc biệt chú trọng đến các cơ hội có thể giúp tiết kiệm nhiệt năng, điện năng.
>> Đánh giá cân bằng nhiệt hệ thống lò nung clinker (P.2)
Để có thể nhận biết được các khả năng này, điều cần thiết là phải đánh giá được một cách chính xác và đầy đủ tình hình sử dụng năng lượng đang diễn ra tại mỗi công đoạn, từ đó mới có thể phát hiện ra những điểm lãng phí, bất hợp lý, đề ra được các giải pháp tiết giảm.
I. Sự cần thiết của công tác kiểm tra, đánh giá cân bằng nhiệt hệ thống lò nung clinker xi măng
Với mỗi dây chuyền sản xuất xi măng, sau một thời gian hoạt động sẽ phát sinh các khác biệt nhất định so với thiết kế ban đầu. Tùy từng dây chuyền cụ thể mà sự sai khác này có thể ở các mức độ khác nhau, nhưng đều có một điểm chung là không còn được như thiết kế ban đầu. Có nhiều nguyên nhân dẫn đến hiện tượng này như sự thay đổi về nguồn nguyên, nhiên liệu, thay đổi về chế độ vận hành, về thiết bị… Đồng thời, sự già cỗi, xuống cấp, lạc hậu, hư hỏng của thiết bị cũng là một lý do gây lên sự sai khác của hệ thống so với thiết kế nguyên bản.
Đặc biệt, tại công đoạn nung luyện clinker điều này rất dễ xảy ra do tính khắc nghiệt của chế độ nung luyện khiến các vị trí hư hại, xuống cấp, rò rỉ khí nóng… xuất hiện ngày càng nhiều theo thời gian. Do đó, việc kiểm tra, đánh giá cân bằng nhiệt của hệ thống lò nung clinker là một việc làm hết sức cần thiết. Việc này có thể tiến hành vừa định kỳ, vừa đột xuất, để có thể ghi nhận kịp thời các thay đổi của hệ thống, phát hiện các điểm thất thoát nhiệt năng, từ đó có biện pháp xử lý phù hợp nhằm mục tiêu giảm tiêu hao nhiên liệu cho công đoạn lò nung.
Thông qua việc kiểm tra, đánh giá cân bằng nhiệt của hệ thống lò nung, các doanh nghiệp sẽ trả lời được hai câu hỏi quan trọng: dây chuyền của mình đang hoạt động như thế nào, và: cần phải làm gì để nó hoạt động tối ưu hơn. Thông qua công tác này, mỗi nhà sản xuất xi măng sẽ tìm thấy cơ hội giảm tiêu hao than, dầu, điện năng trên một đơn vị sản phẩm, giảm chi phí sửa chữa, bảo dưỡng thiết bị, góp phần giảm giá thành sản phẩm, nâng cao sức cạnh tranh của doanh nghiệp, giảm khí thải độc hại phát thải ra môi trường.
II. Các nội dung cơ bản của công tác kiểm tra, đánh giá cân bằng nhiệt hệ thống lò nung
Quy trình kiểm tra, đánh giá cân bằng nhiệt của hệ thống lò nung có thể được thực hiện theo các bước như sau:
- Đo đạc, thu thập số liệu vận hành thực tế trong các giai đoạn trước đây và hiện nay về:
+ Các thông số quá trình, đo lường khí, gas
+ Dữ liệu về nguyên liệu, bột liệu, clinker, than, dầu
+ Dữ liệu về quá trình đốt nhiên liệu tại lò, calciner
+ Dữ liệu theo thiết kế của nhà cung cấp
- Tính toán cân bằng nhiệt của hệ thống
- So sánh với thiết kế ban đầu và với các dây chuyền tương tự
- Nhận xét, đánh giá và đề ra giải pháp khắc phục.
- Tổ chức thực hiện giải pháp, đánh giá hiệu quả thực tế thu được
- Tái kiểm tra theo chu trình liên tục
1. Đo đạc, thu thập số liệu
Để có thể tính toán cân bằng nhiệt của hệ thống lò, đầu tiên cần phải có đầy đủ các số liệu cần thiết. Đó là các thông số đầu vào của bài toán cân bằng nhiệt như: năng suất cấp liệu lò, tỷ lệ đốt than mịn tại lò và Calciner, lưu lượng các quạt trong hệ thống (các quạt gió 1, quạt làm mát clinker thổi vào cooler, quạt ID…), lưu lượng, nhiệt độ gió 2, gió 3… Với mỗi yếu tố này, cần thu thập đầy đủ các thông số liên quan cho việc tính toán như: nhiệt độ, áp suất, nhiệt dung riêng, đường kính đường ống, tỷ trọng riêng…
Trong các thông số này, có những thông số có thể quan sát trực tiếp được từ màn hình vận hành tại phòng điều khiển trung tâm, số khác phải đọc trực tiếp trên các thiết bị đo lường gắn trên thiết bị, hoặc đo đạc trực tiếp bằng các thiết bị chuyên dụng. Các thông số có tính cố định, có sẵn như đường kính các đường ống, tỷ trọng riêng…sẽ thu thập được từ tài liệu thiết kế, lắp đặt khi xây dựng nhà máy. Ngoài ra, cũng có nhiều thông số phải tự tính toán hoặc tra bảng, lựa chọn (giả định) dựa trên các thông số khác, như nhiệt dung riêng của vật chất, hay các hệ số trong công thức tính.
2. Tính toán cân bằng nhiệt của hệ thống
Việc tính toán được thực hiện chủ yếu theo các công thức lý thuyết vốn đã rất phổ biến và quen thuộc đối với các kỹ sư làm việc trong ngành xi măng, nên người viết không nêu lại chi tiết cách tính. Hiện nay, có nhiều phần mềm khác nhau để tính toán bài toán cân bằng nhiệt này, nhưng nhìn chung, tất cả đều dựa trên những công thức tính lý thuyết chung về nhiệt lượng của từng yếu tố vật chất (liệu, than, khí, clinker …) mang vào và mang ra khỏi hệ thống lò.
Một số hãng có truyền thống hoạt động lâu năm trong công nghiệp xi măng như FLSmidth, Holcim…cũng giới thiệu thêm một số công thức theo kinh nghiệm riêng của họ, với nhiều hệ số tính toán thực nghiệm được đúc rút từ nhiều lần tính toán trên các dây chuyền khác nhau.
Hiện nay, Công ty tư vấn đầu tư phát triển xi măng (CCID) cũng đang triển khai đề tài xây dựng phần mềm tính toán thiết kế tổng thể toàn nhà máy, trong đó có việc tính toán cân bằng nhiệt của hệ thống lò nung. Phần mềm này không những là công cụ phục vụ thiết kế một dây chuyền mới, mà còn có thể dùng để kiểm tra các dây chuyền đang hoạt động, dựa trên các thông số vận hành thực tế. Phần mềm hiện đang trong giai đoạn chạy thử nghiệm và dự kiến khi hoàn thành, sẽ được phổ biến áp dụng cho việc tính toán kiểm tra cân bằng nhiệt của các đơn vị thành viên Vicem.
3. So sánh với thiết kế ban đầu và với các dây chuyền tương tự
Sau khi hoàn thành bài tính cân bằng nhiệt, chúng ta có thể dễ dàng nhận ra tình trạng của hệ thống lò. Đặc biệt, khi tiến hành so sánh với tài liệu thiết kế ban đầu của chính dây chuyền này, mọi sự sai khác sẽ thể hiện rất rõ. Như đã nói ở phần trên, trong quá trình hoạt động, vì nhiều lý do khác nhau mà rất hiếm dây chuyền sản xuất nào có thể hoạt động được đúng như các thông số thiết kế ban đầu. Mức độ sai lệch này sẽ được phản ánh cụ thể qua nhiều thông số, đặc biệt là tại công đoạn lò: nhiệt độ gió 2, gió 3, tiêu hao nhiệt năng trên một đơn vị sản phẩm, nhiệt độ clinker ra khỏi bộ làm mát, năng suất lò, nhiệt độ, thành phần khí thải…
Nếu có thể thu thập được các thông số của một dây chuyền tương tự (về công suất, thiết bị, trình độ tiên tiến…) và tiến hành so sánh, sẽ giúp những người đang trực tiếp vận hành nhà máy cũng như đội ngũ quản lý có cái nhìn khách quan, toàn diện hơn về dây chuyền của mình. Những số liệu này khi được đặt cạnh nhau, sẽ cho thấy rõ nét nhất về hiện trạng của công đoạn: gần với thiết kế nhất, sai lệch trong phạm vi chấp nhận được, hay đang bị sai lệch quá nhiều so với thiết kế hoặc với dây chuyền tương tự. Một số chỉ tiêu có thể tốt hơn, ví dụ như năng suất thực tế của lò sẽ cao hơn năng suất thiết kế, nhiệt độ, nồng độ khí thải thấp hơn thiết kế… nhưng cũng sẽ có những chỉ tiêu thay đổi theo chiều hướng xấu như tăng tiêu hao nhiệt năng riêng, tăng tiêu hao khí làm mát, nhiệt độ clinker cao hơn thiết kế…
4. Nhận xét, đánh giá và đề ra giải pháp
Nếu như các bước đo đạc, tính toán và so sánh kể trên được coi là khâu “khám bệnh” cho hệ thống lò, thì việc nhận xét, đánh giá và đề ra giải pháp sẽ có vai trò quan trọng như việc chỉ ra nguyên nhân và cách điều trị cho các chứng bệnh đó. Đó có thể là các nguyên nhân khách quan, như sự thay đổi về nguồn nguyên, nhiên liệu, sự xuống cấp, lão hóa của thiết bị… Cũng có nhiều nguyên nhân chủ quan như: ý thức, trình độ vận hành chưa cao, công tác kiểm tra phát hiện sớm sự cố, bảo dưỡng, sửa chữa thiết bị chưa đảm bảo.
Khi các nguyên nhân đã được phân tích, mổ xẻ và thống nhất cao, thì việc đề ra giải pháp thường không quá khó khăn. Với các khuyết điểm đang tồn tại, sẽ có hai hướng giải quyết cơ bản: đưa trở về thiết kế nguyên bản, hoặc cải tiến, cải tạo theo hướng tối ưu hơn. Trước tiên, các giải pháp cần được xem xét ở mức độ tối ưu nhất về mặt kỹ thuật. Tùy đặc điểm của từng nhà máy, các yếu tố khác như kinh tế, tài chính, quản lý sẽ được tính đến, để cuối cùng có thể lựa chọn được giải pháp hoàn hảo nhất, đem lại lợi ích to lớn nhất cho do- anh nghiệp.
5. Tổ chức thực hiện giải pháp, đánh giá hiệu quả thực tế thu được
Việc tổ chức thực hiện giải pháp có thể tiến hành đồng thời, hoặc chia làm nhiều giai đoạn khác nhau, căn cứ vào tình hình sản xuất - kinh doanh của các đơn vị. Cần có kế hoạch cụ thể, chi tiết cho việc thực hiện này, và tránh tình trạng thực hiện nửa vời hay kéo dài các nội dung tổng thể trong một thời gian quá lâu. Giải pháp đã đề ra chỉ thực sự phát huy được hiệu quả như mong đợi nếu tất cả các nội dung của nó được thực hiện một cách đồng bộ.
Ví dụ: khó có thể giảm được lượng than tiêu hao cho hệ thống lò, nếu các vị trí rò rỉ khí nóng và khí lạnh thâm nhập chưa được xử lý. Nhiệt độ clinker ra khỏi thiết bị làm mát cũng không thể hạ thấp nếu các quạt cooler chưa cung cấp đủ lượng gió cần thiết. Điều này sẽ ảnh hưởng ngược lại đến nhiệt độ gió 3 đi lên tháp sấy, từ đó tác động đến lượng than tiêu hao cho lò, tạo thành một vòng luẩn quẩn, móc xích lẫn nhau.
Đánh giá hiệu quả của giải pháp: Sau một thời gian áp dụng, cần có sự đánh giá các giải pháp để kịp thời ghi nhận hiệu quả của nó, có sự điều chỉnh kịp thời nếu cần. Dựa vào các thông số vận hành chủ yếu trước và sau khi điều chỉnh trong một khoảng thời gian nhất định, sẽ dễ dàng nhận thấy mức độ tác động của biện pháp này, từ đó có thể kết luận về tính hiệu quả của nó.
Khi đưa ra giải pháp, có thể chúng ta đã không thể dự báo được hết tất cả các tác động của nó đối với dây chuyền, và bây giờ là thời điểm tốt nhất để nhìn nhận lại một cách toàn diện hơn. Điều này còn mang ý nghĩa quan trọng trong việc lập lên một cơ sở dữ liệu về hệ thống, khi mọi thay đổi đều được ghi nhận một cách đầy đủ, chi tiết. Theo thời gian, cơ sở dữ liệu này sẽ ngày càng đầy đủ và phong phú, từ đó giúp người vận hành có thể dễ dàng phán đoán đúng về tình trạng của hệ thống mỗi khi quyết định can thiệp thay đổi một điều gì đó liên quan đến hoạt động của chúng.
6. Thực hiện liên tục quy trình
Thực tế sản xuất luôn chứa đựng nhiều yếu tố có thể làm thay đổi tình trạng hoạt động của hệ thống, vì vậy quy trình đánh giá này cần phải được thực hiện thường xuyên, liên tục. Sau khi đã xử lý xong một vấn đề, các vấn đề khác lại có thể tiếp tục phát sinh. Đặc biệt, tại các thời điểm quan trọng như hệ thống lò mới được sửa chữa lớn, hoặc đang gặp phải một sự cố nghiêm trọng, chưa thể khắc phục ngay trong thời gian ngắn thì điều này càng có ý nghĩa. Kịp thời kiểm tra, đánh giá tình trạng, đưa ra giải pháp để hệ thống hoạt động tối ưu, dù chỉ là trong một giai đoạn nhất định có tính tạm thời.
Để có thể nhận biết được các khả năng này, điều cần thiết là phải đánh giá được một cách chính xác và đầy đủ tình hình sử dụng năng lượng đang diễn ra tại mỗi công đoạn, từ đó mới có thể phát hiện ra những điểm lãng phí, bất hợp lý, đề ra được các giải pháp tiết giảm.
I. Sự cần thiết của công tác kiểm tra, đánh giá cân bằng nhiệt hệ thống lò nung clinker xi măng
Với mỗi dây chuyền sản xuất xi măng, sau một thời gian hoạt động sẽ phát sinh các khác biệt nhất định so với thiết kế ban đầu. Tùy từng dây chuyền cụ thể mà sự sai khác này có thể ở các mức độ khác nhau, nhưng đều có một điểm chung là không còn được như thiết kế ban đầu. Có nhiều nguyên nhân dẫn đến hiện tượng này như sự thay đổi về nguồn nguyên, nhiên liệu, thay đổi về chế độ vận hành, về thiết bị… Đồng thời, sự già cỗi, xuống cấp, lạc hậu, hư hỏng của thiết bị cũng là một lý do gây lên sự sai khác của hệ thống so với thiết kế nguyên bản.
Đặc biệt, tại công đoạn nung luyện clinker điều này rất dễ xảy ra do tính khắc nghiệt của chế độ nung luyện khiến các vị trí hư hại, xuống cấp, rò rỉ khí nóng… xuất hiện ngày càng nhiều theo thời gian. Do đó, việc kiểm tra, đánh giá cân bằng nhiệt của hệ thống lò nung clinker là một việc làm hết sức cần thiết. Việc này có thể tiến hành vừa định kỳ, vừa đột xuất, để có thể ghi nhận kịp thời các thay đổi của hệ thống, phát hiện các điểm thất thoát nhiệt năng, từ đó có biện pháp xử lý phù hợp nhằm mục tiêu giảm tiêu hao nhiên liệu cho công đoạn lò nung.
Thông qua việc kiểm tra, đánh giá cân bằng nhiệt của hệ thống lò nung, các doanh nghiệp sẽ trả lời được hai câu hỏi quan trọng: dây chuyền của mình đang hoạt động như thế nào, và: cần phải làm gì để nó hoạt động tối ưu hơn. Thông qua công tác này, mỗi nhà sản xuất xi măng sẽ tìm thấy cơ hội giảm tiêu hao than, dầu, điện năng trên một đơn vị sản phẩm, giảm chi phí sửa chữa, bảo dưỡng thiết bị, góp phần giảm giá thành sản phẩm, nâng cao sức cạnh tranh của doanh nghiệp, giảm khí thải độc hại phát thải ra môi trường.
II. Các nội dung cơ bản của công tác kiểm tra, đánh giá cân bằng nhiệt hệ thống lò nung
Quy trình kiểm tra, đánh giá cân bằng nhiệt của hệ thống lò nung có thể được thực hiện theo các bước như sau:
- Đo đạc, thu thập số liệu vận hành thực tế trong các giai đoạn trước đây và hiện nay về:
+ Các thông số quá trình, đo lường khí, gas
+ Dữ liệu về nguyên liệu, bột liệu, clinker, than, dầu
+ Dữ liệu về quá trình đốt nhiên liệu tại lò, calciner
+ Dữ liệu theo thiết kế của nhà cung cấp
- Tính toán cân bằng nhiệt của hệ thống
- So sánh với thiết kế ban đầu và với các dây chuyền tương tự
- Nhận xét, đánh giá và đề ra giải pháp khắc phục.
- Tổ chức thực hiện giải pháp, đánh giá hiệu quả thực tế thu được
- Tái kiểm tra theo chu trình liên tục
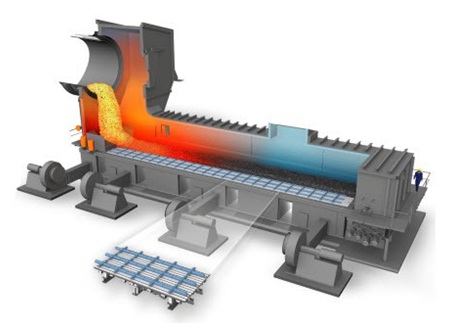
1. Đo đạc, thu thập số liệu
Để có thể tính toán cân bằng nhiệt của hệ thống lò, đầu tiên cần phải có đầy đủ các số liệu cần thiết. Đó là các thông số đầu vào của bài toán cân bằng nhiệt như: năng suất cấp liệu lò, tỷ lệ đốt than mịn tại lò và Calciner, lưu lượng các quạt trong hệ thống (các quạt gió 1, quạt làm mát clinker thổi vào cooler, quạt ID…), lưu lượng, nhiệt độ gió 2, gió 3… Với mỗi yếu tố này, cần thu thập đầy đủ các thông số liên quan cho việc tính toán như: nhiệt độ, áp suất, nhiệt dung riêng, đường kính đường ống, tỷ trọng riêng…
Trong các thông số này, có những thông số có thể quan sát trực tiếp được từ màn hình vận hành tại phòng điều khiển trung tâm, số khác phải đọc trực tiếp trên các thiết bị đo lường gắn trên thiết bị, hoặc đo đạc trực tiếp bằng các thiết bị chuyên dụng. Các thông số có tính cố định, có sẵn như đường kính các đường ống, tỷ trọng riêng…sẽ thu thập được từ tài liệu thiết kế, lắp đặt khi xây dựng nhà máy. Ngoài ra, cũng có nhiều thông số phải tự tính toán hoặc tra bảng, lựa chọn (giả định) dựa trên các thông số khác, như nhiệt dung riêng của vật chất, hay các hệ số trong công thức tính.
2. Tính toán cân bằng nhiệt của hệ thống
Việc tính toán được thực hiện chủ yếu theo các công thức lý thuyết vốn đã rất phổ biến và quen thuộc đối với các kỹ sư làm việc trong ngành xi măng, nên người viết không nêu lại chi tiết cách tính. Hiện nay, có nhiều phần mềm khác nhau để tính toán bài toán cân bằng nhiệt này, nhưng nhìn chung, tất cả đều dựa trên những công thức tính lý thuyết chung về nhiệt lượng của từng yếu tố vật chất (liệu, than, khí, clinker …) mang vào và mang ra khỏi hệ thống lò.
Một số hãng có truyền thống hoạt động lâu năm trong công nghiệp xi măng như FLSmidth, Holcim…cũng giới thiệu thêm một số công thức theo kinh nghiệm riêng của họ, với nhiều hệ số tính toán thực nghiệm được đúc rút từ nhiều lần tính toán trên các dây chuyền khác nhau.
Hiện nay, Công ty tư vấn đầu tư phát triển xi măng (CCID) cũng đang triển khai đề tài xây dựng phần mềm tính toán thiết kế tổng thể toàn nhà máy, trong đó có việc tính toán cân bằng nhiệt của hệ thống lò nung. Phần mềm này không những là công cụ phục vụ thiết kế một dây chuyền mới, mà còn có thể dùng để kiểm tra các dây chuyền đang hoạt động, dựa trên các thông số vận hành thực tế. Phần mềm hiện đang trong giai đoạn chạy thử nghiệm và dự kiến khi hoàn thành, sẽ được phổ biến áp dụng cho việc tính toán kiểm tra cân bằng nhiệt của các đơn vị thành viên Vicem.
3. So sánh với thiết kế ban đầu và với các dây chuyền tương tự
Sau khi hoàn thành bài tính cân bằng nhiệt, chúng ta có thể dễ dàng nhận ra tình trạng của hệ thống lò. Đặc biệt, khi tiến hành so sánh với tài liệu thiết kế ban đầu của chính dây chuyền này, mọi sự sai khác sẽ thể hiện rất rõ. Như đã nói ở phần trên, trong quá trình hoạt động, vì nhiều lý do khác nhau mà rất hiếm dây chuyền sản xuất nào có thể hoạt động được đúng như các thông số thiết kế ban đầu. Mức độ sai lệch này sẽ được phản ánh cụ thể qua nhiều thông số, đặc biệt là tại công đoạn lò: nhiệt độ gió 2, gió 3, tiêu hao nhiệt năng trên một đơn vị sản phẩm, nhiệt độ clinker ra khỏi bộ làm mát, năng suất lò, nhiệt độ, thành phần khí thải…
Nếu có thể thu thập được các thông số của một dây chuyền tương tự (về công suất, thiết bị, trình độ tiên tiến…) và tiến hành so sánh, sẽ giúp những người đang trực tiếp vận hành nhà máy cũng như đội ngũ quản lý có cái nhìn khách quan, toàn diện hơn về dây chuyền của mình. Những số liệu này khi được đặt cạnh nhau, sẽ cho thấy rõ nét nhất về hiện trạng của công đoạn: gần với thiết kế nhất, sai lệch trong phạm vi chấp nhận được, hay đang bị sai lệch quá nhiều so với thiết kế hoặc với dây chuyền tương tự. Một số chỉ tiêu có thể tốt hơn, ví dụ như năng suất thực tế của lò sẽ cao hơn năng suất thiết kế, nhiệt độ, nồng độ khí thải thấp hơn thiết kế… nhưng cũng sẽ có những chỉ tiêu thay đổi theo chiều hướng xấu như tăng tiêu hao nhiệt năng riêng, tăng tiêu hao khí làm mát, nhiệt độ clinker cao hơn thiết kế…
4. Nhận xét, đánh giá và đề ra giải pháp
Nếu như các bước đo đạc, tính toán và so sánh kể trên được coi là khâu “khám bệnh” cho hệ thống lò, thì việc nhận xét, đánh giá và đề ra giải pháp sẽ có vai trò quan trọng như việc chỉ ra nguyên nhân và cách điều trị cho các chứng bệnh đó. Đó có thể là các nguyên nhân khách quan, như sự thay đổi về nguồn nguyên, nhiên liệu, sự xuống cấp, lão hóa của thiết bị… Cũng có nhiều nguyên nhân chủ quan như: ý thức, trình độ vận hành chưa cao, công tác kiểm tra phát hiện sớm sự cố, bảo dưỡng, sửa chữa thiết bị chưa đảm bảo.
Khi các nguyên nhân đã được phân tích, mổ xẻ và thống nhất cao, thì việc đề ra giải pháp thường không quá khó khăn. Với các khuyết điểm đang tồn tại, sẽ có hai hướng giải quyết cơ bản: đưa trở về thiết kế nguyên bản, hoặc cải tiến, cải tạo theo hướng tối ưu hơn. Trước tiên, các giải pháp cần được xem xét ở mức độ tối ưu nhất về mặt kỹ thuật. Tùy đặc điểm của từng nhà máy, các yếu tố khác như kinh tế, tài chính, quản lý sẽ được tính đến, để cuối cùng có thể lựa chọn được giải pháp hoàn hảo nhất, đem lại lợi ích to lớn nhất cho do- anh nghiệp.
5. Tổ chức thực hiện giải pháp, đánh giá hiệu quả thực tế thu được
Việc tổ chức thực hiện giải pháp có thể tiến hành đồng thời, hoặc chia làm nhiều giai đoạn khác nhau, căn cứ vào tình hình sản xuất - kinh doanh của các đơn vị. Cần có kế hoạch cụ thể, chi tiết cho việc thực hiện này, và tránh tình trạng thực hiện nửa vời hay kéo dài các nội dung tổng thể trong một thời gian quá lâu. Giải pháp đã đề ra chỉ thực sự phát huy được hiệu quả như mong đợi nếu tất cả các nội dung của nó được thực hiện một cách đồng bộ.
Ví dụ: khó có thể giảm được lượng than tiêu hao cho hệ thống lò, nếu các vị trí rò rỉ khí nóng và khí lạnh thâm nhập chưa được xử lý. Nhiệt độ clinker ra khỏi thiết bị làm mát cũng không thể hạ thấp nếu các quạt cooler chưa cung cấp đủ lượng gió cần thiết. Điều này sẽ ảnh hưởng ngược lại đến nhiệt độ gió 3 đi lên tháp sấy, từ đó tác động đến lượng than tiêu hao cho lò, tạo thành một vòng luẩn quẩn, móc xích lẫn nhau.
Đánh giá hiệu quả của giải pháp: Sau một thời gian áp dụng, cần có sự đánh giá các giải pháp để kịp thời ghi nhận hiệu quả của nó, có sự điều chỉnh kịp thời nếu cần. Dựa vào các thông số vận hành chủ yếu trước và sau khi điều chỉnh trong một khoảng thời gian nhất định, sẽ dễ dàng nhận thấy mức độ tác động của biện pháp này, từ đó có thể kết luận về tính hiệu quả của nó.
Khi đưa ra giải pháp, có thể chúng ta đã không thể dự báo được hết tất cả các tác động của nó đối với dây chuyền, và bây giờ là thời điểm tốt nhất để nhìn nhận lại một cách toàn diện hơn. Điều này còn mang ý nghĩa quan trọng trong việc lập lên một cơ sở dữ liệu về hệ thống, khi mọi thay đổi đều được ghi nhận một cách đầy đủ, chi tiết. Theo thời gian, cơ sở dữ liệu này sẽ ngày càng đầy đủ và phong phú, từ đó giúp người vận hành có thể dễ dàng phán đoán đúng về tình trạng của hệ thống mỗi khi quyết định can thiệp thay đổi một điều gì đó liên quan đến hoạt động của chúng.
6. Thực hiện liên tục quy trình
Thực tế sản xuất luôn chứa đựng nhiều yếu tố có thể làm thay đổi tình trạng hoạt động của hệ thống, vì vậy quy trình đánh giá này cần phải được thực hiện thường xuyên, liên tục. Sau khi đã xử lý xong một vấn đề, các vấn đề khác lại có thể tiếp tục phát sinh. Đặc biệt, tại các thời điểm quan trọng như hệ thống lò mới được sửa chữa lớn, hoặc đang gặp phải một sự cố nghiêm trọng, chưa thể khắc phục ngay trong thời gian ngắn thì điều này càng có ý nghĩa. Kịp thời kiểm tra, đánh giá tình trạng, đưa ra giải pháp để hệ thống hoạt động tối ưu, dù chỉ là trong một giai đoạn nhất định có tính tạm thời.
ximang.vn (Theo Tạp chí KHKT xi măng)